Interview
McLaren Applied’s IPG5-x: A new silicon carbide inverter
Described as ‘the brain of an EV’, McLaren Applied has unveiled a new silicon carbide inverter to assist the automotive EV space. Frankie Youd speaks to McLaren Applied Head of Product, Paolo Bargiacchi to learn more.
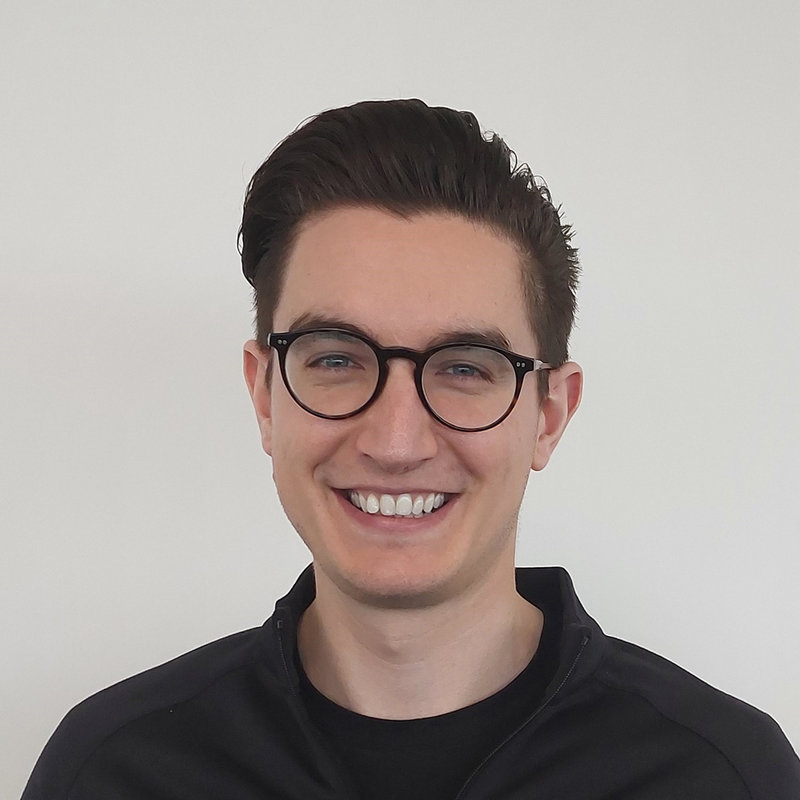
Paolo Bargiacchi, Head of Product, McLaren Applied
McLaren Applied has recently unveiled a new silicon carbide (SiC) inverter IPG5-x, described as a highly flexible inverter platform which can be integrated into electric drive units (EDUs). With a goal to target growing OEM demand for integrated, high-performing EDUs which save space and cost, McLaren Applied has developed the IPG5-x to operate with a variety of transmissions and motors.
The IPG5-x acts as an adapted evolution of McLaren Applied’s standalone 800V SiC inverter, IPG5, and will co-exist alongside.
Frankie Youd spoke to Paolo Bargiacchi, head of product at McLaren Applied, to learn more about the new inverter, and to discuss the benefits it will bring to the automotive market.
Frankie Youd: Can you describe your past and your current role?
Paolo Bargiacchi: I’ve been with McLaren Applied for about three years now. Prior to that, I was on the OEM side, always in automotive.
I started out in engineering at Jaguar Land Rover (JLR) in powertrain R&D, before moving to various commercial and product management roles with a focus on the strategic transition to electrification. Following JLR, I had a stint at Bentley Motors in product management, working on their Mulliner division, which is their special vehicles portfolio.
It’s been really interesting to join the team on the supply side of the equation and have a different perspective on the electrification transition. It’s been refreshing to work on technology that goes across a variety of vehicles and industries.
My role in the company is to lead our inverter development team to deliver for to our customers.. That means working with our customers to understand what their needs and requirements are and then also working with our chief engineers to understand the technology roadmaps.
We are also trying to anticipate what customer’s needs might be in the future before they’re really thinking about them. Then we process all of that into our product strategy and product roadmap. One of the challenges is that we’re focused on what’s already at the cutting edge; so how do we push the frontier further? That’s an exciting challenge.
Frankie Youd: Could you discuss the new inverter?
Paolo Bargiacchi: In terms of electrification, the IPG5-x is our progress statement, mostly within what we term as ‘wave three’ in terms of EV tech.
Wave one was the early pioneers like the Tesla Roadster. That introduced electrification. Wave two was the OEM rush to market with all kinds of legacy platform and architectures, so technology-wise, that was the 400-volt IGBT (insulated-gate bipolar transistor) in terms of the power electronics. Wave three has been all about consolidating efficiency, with dedicated EV architectures and further innovations such as the 800-volt silicon carbide power electronics.
Going forward we see an increasing demand for integration from a perspective of more maturity on the powertrain planning side, and understanding how systems can be better optimised.
Going forward we see an increasing demand for integration from a perspective of more maturity on the powertrain planning side, and understanding how systems can be better optimised. For us, what that means is more tightly integrating with the motor and the transmission to form complete electric drive units or EDUs.
What we’ve done with IPG5-x is we’ve taken the maturity level of the IPG5 platform – both the hardware and software – as a starting point. We’ve worked hard on increasing the flexibility and the modularity of the design. It’s going both directly to OEMs or to other Tier 1 partners like transmissions and motor suppliers. Every single application is different and everyone’s got particular package constraints.
What we’ve really tried to do is focus on how we can offer something that moulds really well to the needs of the customer, whoever that may be. In doing so, we aim to bridge the gaps, connections, and optimization levels, particularly between the motor and the inverter, because that’s where all the synergies currently are with the inverter being the main control unit for the motor.
Frankie Youd: How is this product differentiated from others on the market?
Paolo Bargiacchi: There’s lots of talk in automotive at the minute about the future being Software-Defined Vehicles (SDVs). I think that’s a big angle for what we see as the fourth wave of electrification. As we’re getting more EVs into market (the Tesla Model Y is a very big seller in Europe) we can see adoption rates picking up. Eventually, we will get to a state where EV is no longer a differentiation in its own right. It’s then a matter of considering what the brand stands for and what differentiates it from other brands’ products.
For us, it’s looking at how can we (with our inverter) have an impact on the powertrain and ultimately the customer experience. That’s about how we can take the motor control to the next level. That can be in several different ways. Take a customer and a brand like Rolls Royce, for example. It is super focused on what we can do to improve refinement. One of the things that our unique variable switching frequency control enables is that you can switch over resonant frequencies in the motor to remove NVH, or even inject noise cancelling harmonics to take this a step further.
At the other end of the spectrum, for more sporting brands – take a Dodge Challenger, for example – there’s a desire to maintain driver engagement, so you can look at injecting harmonics to augment the natural motor sound, adding some vocal character back in, something which is arguably lacking in many EVs today.
Frankie Youd: Why is there a growing demand from OEMs for EDUs that save space?
Paolo Bargiacchi: One of the classic constraints of any vehicle manufacturer is the package requirements. It’s always a trade-off between design and the different engineering functions.
The OEM will generally want the biggest interior space possible so that customers can be comfortable, but then the engineering function that’s responsible for vehicle efficiency will want the smallest car and package to deliver a certain range or performance. It’s always a trade-off.
OEMs are always looking for how can we minimise the size of our components. One of the options was having components separated to get to market fast.

Caption. Credit:
However, when you go to integration on the electric drive unit itself, you’re able to delete a lot of componentry and make the overall combination much smaller. For example, between the motor and the inverter, you get rid of connectors and cables, and instead you can just have direct busbar connections.
You’ve then got the unit itself, which will be much smaller and easier to package, and there are the efficiency benefits of silicon carbide – it means your cooling system can be downsized. It also means you can downsize your battery and maintain the same range.
The battery is the single biggest, heaviest, most expensive and most carbon intensive part in the electric vehicle. There is lots of embedded energy in the battery. In the end, it’s about the virtuous cycle of efficiency not only for electric drive unit, but all the powertrain components around it. That means you can effectively shrink-wrap the entire chassis and the whole vehicle around that as well. There are many knock-on benefits.
Frankie Youd: What is the current timeline for the new inverter?
Paolo Bargiacchi: With the IPG5, we’ve been scaling up now over a number of years working through our prototype samples and that’s going into a more high-volume production for 2025. What we’ve focused on with the IPG5-x programme is a fast to market approach. We are trying to use as much commonality with the IPG5 platform that we’ve already built and the product development maturity there, so actually we’re going to be offering the IPG5-x inverter within 2025 as well, depending on application.
One of the plus points of having this flexibility and modularity means we can get the baseline product to market quicker, but also each application development with different customers or partners for a new EDU is also going to be on a much shorter timeframe, which means it’s more cost-effective as well.
Frankie Youd: What do you see the roadmap looking like for the automotive space over the new few years?
Paolo Bargiacchi: We’re getting real adoption from all the OEMs when it comes to silicon carbide and that is now pushing the technology landscape more quickly.
We work closely with our suppliers, and looking at their technology roadmaps we can see now that the hardware is almost on a two-to-three-year cycle of big step-changes in performance. For us, we absolutely need to maintain that leadership position on what we see as the cutting edge. It means working very closely with them, making sure we’ve got the key component updates we need.
We’ve seen all sorts of high investments all through the supply chain, with companies putting billions into new manufacturing plants, new devices, new technological advancements. What that means for us in terms of our product roadmap is that we must keep up.
We’ll be looking at similarly doing highly iterative product development cycles to ensure that we’re always using the latest and best hardware in combination with our market-leading software.
From a broader angle, I think there’s going to be even more integration at different levels. Today, the integration focus is very much between the motor and the inverter, but there are other components on the vehicle that would benefit from integration with the inverter, such as DC-DC, OBC etc. This will give more benefits in terms of cost, efficiency, packaging and other design improvements.
Outside of that, one of the other big trends that we do see starting to emerge is magnet-free motors. There’s lots of focus on sustainability, but also supply chain volatility and risk mitigation – there’s a heavy reliance on China for certain raw materials and mining itself is quite a carbon intensive process.
There is quite a bit of work going on for magnet-free solutions. That requires additional control in the inverter that effectively then replicates the magnetic flux from the permanent magnet; you can do that purely with electronics. If you can strip the permanent magnets out of the motor build, it is good for cost and also sustainability and supply chain volatility. It reduces that reliance on just one market for the source materials. That’s another big technology transition that we can see developing over time.