Heads-up Displays: Measurements and Safety Aspects
Radiant Vision Systems (RVS), since 2015 part of Konica Minolta Sensing Business Unit, is a technological leader in advanced imaging systems to evaluate light, color, manufacturing integrity and surface quality of displays and lightings. Alongside the rapid technological changes in the Automotive Industry, RVS has been focusing on developing next generation solutions for Quality Assurance for Central Cluster-, Head-up- Infotainment-Displays and Car Monitoring Systems (Digital Rear-view Display) Dr. Kedar Sathaye, Head of Application Light & Display at Konica Minolta Sensing Europe, shed light on the challenges and solutions for HUDs
HUDs Today and tomorrow
Today's and future vehicles, high resolution displays show wealth of data from car's speed, navigation to onboard entertainment. These displays not only improve the experience but also provide the driver with required safety on the road by alerting them on dangers ahead. HUDs offer a unique way of displaying information such as speed, navigation and situational alerts onto the windscreen so the driver concentration remain assured at all times. With new technologies such as 3D and AR (Augmented Reality), HUDs are forecasted to be among the highest growing technology in automotive market with compound annual growth rate at over 20%.
3D and AR, HUDs are forecasted to be among the highest growing new technology in future automotive vehicles
New technologies bring new challenges
Head up displays can be divided in two types: Fixed distance and variable distance. The first type can further be divided into two subtypes; display based and projection based. While the variable distance based HUDs are the next generation HUDs where the sophisticated techniques like AR and 3D is used to project an image. In the fixed distance HUDs, the information is being displayed on a transparent display in the driver's view or the information is being projected on to the windshield by different projection techniques. The common thread being that the information is always presented at a fixed distance or in other words in the same focal plane. Because the projections appear at a fixed depth, the focal distance from a virtual image to an object on the road may vary considerably. This requires the driver to shift visual focus from the HUD to the road and back, limiting response time to scenarios outside the vehicle. To overcome these limitations of traditional HUDs, AR-HUDs use data obtained from different sensors on the outside of the vehicle to correctly map projected images to the positions and focal distances of real objects in the environment.
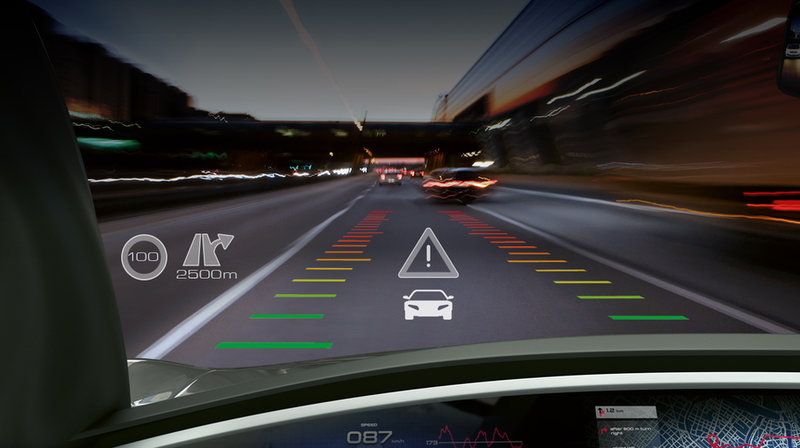
Augmented Reality 3D HUDs of next generation cars enhance driver experience and security
Ensuring quality standards and safety aspects
OEM’s are interested in the solution where the HUD is integrated into car. Having such a solution in the car requires them to follow certain quality standards as poor-quality pose a risk to consumers. In order to eliminate those risks, automotive standards for HUD performance have been established to ensure that manufacturers evaluate HUDs to baseline thresholds for quality and safety. These safety implications of HUD quality have motivated OEM’s test and measurement equipment to partner with the Society of Automotive Engineers (SAE) Committee to define standard measurement criteria to assess the quality of HUDs in accordance to standards SAE J1757-1 and ISO 15008. The new standard (SAE J1757-2 “Optical Metrology for Automotive HUD”), published in 2017, provides a methodology for optical measurement geometries and requirements for measuring vehicle HUDs, including the performance of AR-HUDs. Standardized test methods will ensure accurate projections of virtual images relative to an operator’s eye (including depth of field (DOF), field of view (FOV), diopter, focus, image location, and image distance), legibility of HUD virtual images in typical ambient light illumination (requiring luminance, chromaticity, uniformity, and contrast testing), and image distortion, aberration, or ghosting measured by point deviation from a target virtual image.
Because HUDs are providing safety-critical information through advanced driver assistance systems (ADAS), they must comply with functional safety standards. Functional safety is an important consideration for displays because, particularly for applications such as ADAS, it is essential that the displays perform reliably while providing the driver with clear images. The functional safety of automotive electronic/electrical systems is directed by ISO 26262. Automotive Safety Integrity Level (ASIL), which classifies the inherent safety risk in an automotive system, is an integral part of that standard. There are four ASIL levels: ASIL A, ASIL B, ASIL C, and ASIL D, with ASIL D being the most stringent. For automotive displays and most notably for HUDs ASIL B compliance is the target.
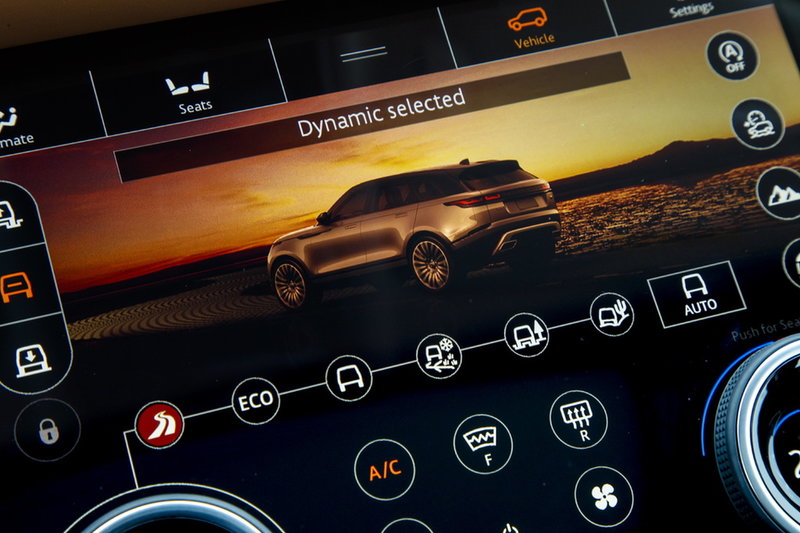
More screens, fewer buttons (Range Rover Velar).
Radiant Vision high resolution imaging photometer provide both, light measurement and visual inspection tools
What makes Radiant Vision System cameras superior for HUD measurements?
In HUD testing, we have 3 different challenges: metrological, geometrical challenges and analysis of full field of view of the HUD. Previously, each of these challenges required a different instrument like spot meters, machine vision cameras and imaging based platform respectively to overcome them. With Radiant Vision high resolution cameras, one can replace all these instruments by incorporating imaging photometers in combination with electronically controlled lens to simplify the HUD test and measurement. Radiant Vision high resolution imaging photometer provide both, light measurement and visual inspection tools. They’re able to capture two-dimensional images of the HUD projection and thus perform all measurements required for SAE HUD evaluation in a single image.
OEMs and Tier 1 suppliers always face different challenges while performing HUD measurements. Some of them include: finding virtual image location and its size, measuring accurate image resolution and contrast, number of tests and parameters per test image and finally enabling production level automated measurements. Radiant Vision use electronically controlled lens to gauge the virtual image size and its location, hence, the lenses remove human calculation and reduce the time to set up the measurements. Electronically controlled lens essentially converts the focal distance into "real distance" units by outputting the distance of projected image through the software.
Complexity of performing different HUD measurements does not only depend on the instrument capabilities and flexibility but also requires sophisticated software, capable performing and analyzing several measurement test sequences at a time. Test sequencing software programs allow distinct measurement criteria, points of interests, and inspection tolerances to be programmed into a series of separate steps within one software environment and then run as a multi-part evaluation of the HUD.
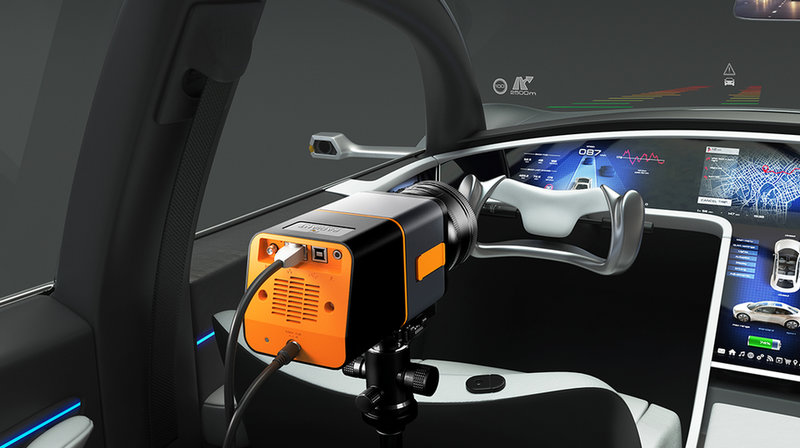
High resolution camera and electronic lens enable measurement of large and curved displays
Outlook
With the rapid growth of more sophisticated HUDs in future vehicles, the demand for efficient measurement systems increasing rapidly. Measurement systems will have to ensure that OEM’s and suppliers achieve compliance. As SAE standard compliance becomes the baseline qualification for HUD selection, the competitive advantage for manufacturers will be the speed and efficiency to produce quality products that ensure optimal value of their technologies. Automated HUD measurement systems including imaging photometers or colorimeters with advanced test sequencing software greatly reduce HUD evaluation time. It will also enable production-level measurement, ensuring compliance, and limiting cost and time to market.
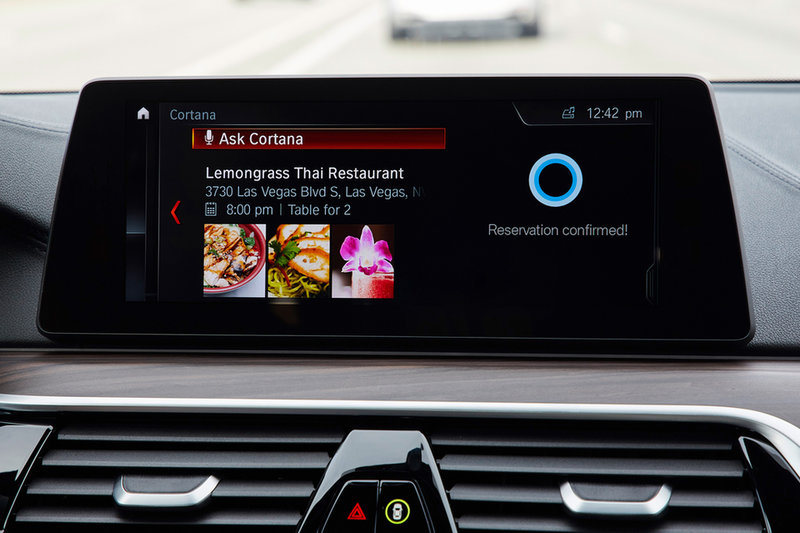
If in doubt, ask: Microsoft’s Cortana AI system forms part of BMW’s Connected Car vision.