Thought leadership
Sponsored by Optitex
How Optitex helped DRÄXLMAIER elevate its standard across the board
DRÄXLMAIER’s company is truly worldwide, with plants in Mexico, China, Romania, Poland and Germany. As you’d expect with a company like this, simplification of processes and production efficiency are key, and just as much - overcoming the language barrier between plants. Here’s how Optitex allowed them to resolve all that and more.
An emergency drill onboard AIDAsol cruise ship in 2019. Image: MikhailBerkut / Shutterstock.com
DRÄXLMAIER’s company is truly worldwide, with plants in Mexico, China, Romania, Poland and Germany. As you’d expect with a company like this, simplification of processes and production efficiency are key, and just as much - overcoming the language barrier between plants. Here’s how Optitex allowed them to resolve all that and more.
We had numbers up to half a million EUR material consumption that we could save. And that was just with already existing pieces that we would reinvest. The potential number with future ranges was even greater.
The first change DRÄXLMAIER, supplier for premium automotive manufacturers worldwide, made was a small but significant one. “IT decided that we had to move on to Windows 10 and our old CAD program was no longer capable of that” says Vanessa Stelzl, Process Development Pattern at DRÄXLMAIER.
So a change was needed, and fast. The company already had experience with Optitex back in 2015, and three years later, DRÄXLMAIER came back to Optitex. One of the key reasons was the ability to use the nesting capabilities that Optitex has.
“We found that we could save so much material that it was would actually be much more beneficial to change to optitex as soon as possible.,” says Stelzl. And the amount was significant, saying “we had numbers up to half a million EUR material consumption that we could save. And that was just with already existing pieces that we would reinvest.” Meaning the potential number with future ranges was even greater.
Another factor was simplification. DRÄXLMAIER’s systems had grown and evolved into something increasingly complex, requiring several systems for export and import.
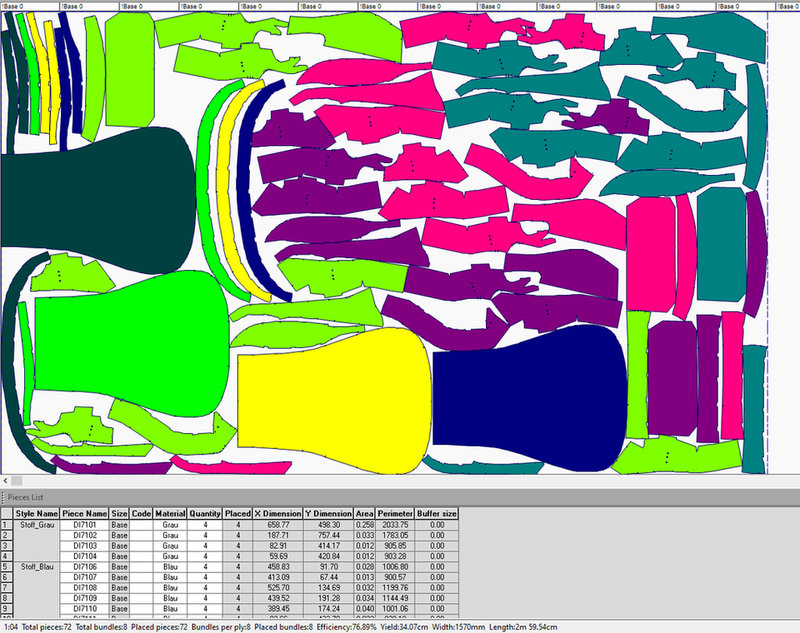
“Previously the third-party programs were only installed on one computer. So you always had to switch computers if you wanted to look at anything. “With Optitex interoperable tools and openness to all cutters in the market, we don't have to switch computers anymore” says Stelzl. Now you can have everything on your computer.” The switch meant that the company had gone from ten programs down to a single - Optitex.
In addition, the speediness of the export feature expedited our work process even further, as DRÄXLMAIER needs to export every file into four different formats.
A large issue with DRÄXLMAIER is one of its biggest strengths, its worldwide presence. The company has plants in Mexico, China, Romania, Poland and Germany amongst others. So the ability to switch languages is important.
“While we all use English at the moment, Optitex users in all our plants have the capability to switch the language if they need help with understanding anything,” says Vanessa Stelzl. “The biggest issue that we faced with our previous system is that because it was such an old program, the translations were not good, that they were not up to date and that we could not communicate between each other because the functions would be named something completely different.” As you’d imagine, a misnamed function could easily lead to miscommunication between plants, something that could be costly in the long run. “So it's helped us on a global level to just speak one language.”
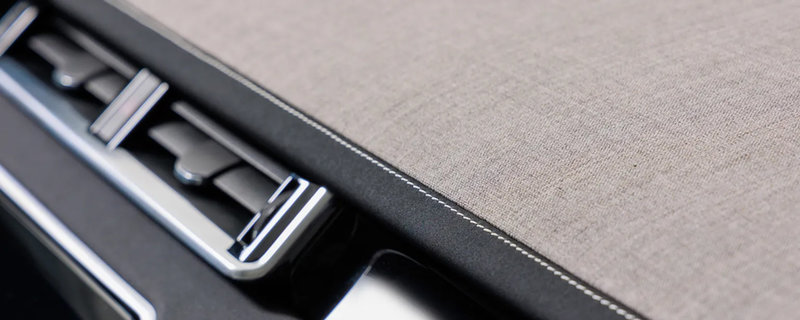
A key aspect of using Optitex for DRÄXLMAIER is that it’s enabled them to elevate the standard across the board. “We've come up to a really high level of pattern making for everybody,” says Stelzl. The software has enabled a levelling of the playing field. “Before we had some who were better, some who were not so good, and now all of them are pretty much on one level.”
The possibilities within Optitex have enabled a different standard of working within the company. “You have endless capabilities and different combinations of functions and the end result may be the same, but I've gotten much faster with patternmaking. It comes more naturally in most cases.”
For DRÄXLMAIER, what started as a simple Windows upgrade led to so much more. Using Optitex’s software has allowed changes and improvements across the board, from the combination of saved costs with nesting, the ability to effectively communicate across production plants globally and the raising of the base level of patternmaking. The end result? A true elevation of the standard for now and the future.
Muster 2.0 removes friction on board
When looking at the new Muster 2.0 drill process in the context of Royal Caribbean’s digital transformation, it is a natural development for a company striving to reduce passenger friction on board.
“The innovative programme is the first of its kind and reimagines a process originally designed for larger groups of people into a faster, more personal approach that encourages higher levels of safety,” says Royal Caribbean’s vice president of sales Ben Bouldin for Europe Middle East and Africa.
The safety drill has always put a pause on the cruise experience
Over the last few years reducing friction has been the focus of Royal Caribbean’s digital department and the goal of the Royal app, which, among other features, allows guests to avoid queues by finding out information and booking dinner tables, activities, excursions and shows online.
In 2018, at the launch of Symphony of the Seas, Royal Caribbean’s senior vice president of digital Jay Schneider explained to Future Cruise that building guest products that “get people out of lines and let people enjoy their vacation first and foremost” has been one of his main missions.
Recently he said that: “Muster 2.0 represents a natural extension of our mission to improve our guests’ vacation experiences by removing points of friction.”
Ben Bouldin is Royal Caribbean’s vice president sales for Europe Middle East and Africa. Image: Royal Caribbean
Schneider and Nick Weir, the senior vice president of entertainment at Royal Caribbean were instrumental to the development of Muster 2.0. Weir is behind some of the most original and innovative entertainment experiences guests can have at sea and has successfully mixed and transitioned formats and blended technology into traditional structures, such as turning an on-board ice rink into laser tag, back again into an ice show with synchronised drones and moving image effects such as those that transform the ice into an emotive Arctic whale scene.
“The safety drill has always put a pause on the cruise experience, and I felt like it could be more efficient,” explains Nick. When he was a cruise director he explains how he was responsible for the welcome party as well as drill announcements which always brought a halt to the fun as guests were starting to enjoy themselves.
“I happened to be outside on one hot, sweaty day during the drill, and I thought why not put it all on a device so it can be done individually and monitored? Technology naturally played a big part, location services on smartphones is essential, and a big team at Royal Caribbean came together to make it happen.”
Muster 2.0 removes friction on board
When looking at the new Muster 2.0 drill process in the context of Royal Caribbean’s digital transformation, it is a natural development for a company striving to reduce passenger friction on board.
“The innovative programme is the first of its kind and reimagines a process originally designed for larger groups of people into a faster, more personal approach that encourages higher levels of safety,” says Royal Caribbean’s vice president of sales Ben Bouldin for Europe Middle East and Africa.
The safety drill has always put a pause on the cruise experience
Over the last few years reducing friction has been the focus of Royal Caribbean’s digital department and the goal of the Royal app, which, among other features, allows guests to avoid queues by finding out information and booking dinner tables, activities, excursions and shows online.
In 2018, at the launch of Symphony of the Seas, Royal Caribbean’s senior vice president of digital Jay Schneider explained to Future Cruise that building guest products that “get people out of lines and let people enjoy their vacation first and foremost” has been one of his main missions.
Recently he said that: “Muster 2.0 represents a natural extension of our mission to improve our guests’ vacation experiences by removing points of friction.”
Ben Bouldin is Royal Caribbean’s vice president sales for Europe Middle East and Africa. Image: Royal Caribbean
Schneider and Nick Weir, the senior vice president of entertainment at Royal Caribbean were instrumental to the development of Muster 2.0. Weir is behind some of the most original and innovative entertainment experiences guests can have at sea and has successfully mixed and transitioned formats and blended technology into traditional structures, such as turning an on-board ice rink into laser tag, back again into an ice show with synchronised drones and moving image effects such as those that transform the ice into an emotive Arctic whale scene.
“The safety drill has always put a pause on the cruise experience, and I felt like it could be more efficient,” explains Nick. When he was a cruise director he explains how he was responsible for the welcome party as well as drill announcements which always brought a halt to the fun as guests were starting to enjoy themselves.
“I happened to be outside on one hot, sweaty day during the drill, and I thought why not put it all on a device so it can be done individually and monitored? Technology naturally played a big part, location services on smartphones is essential, and a big team at Royal Caribbean came together to make it happen.”