No-one wants to contemplate an automobile accident, but if it's a risk (and it is) then we want the best technologies available to either avoid it altogether or - if it happens - reduce the worst of the impact consequences for the people involved.
Although the car is built from many different materials, its main structure – known as the body in white (BIW) – is usually made of steel pressings welded together to form a strong and stiff frame. According to Tata Steel, this method of construction accounts for 99.9 per cent of all cars produced in the world. The remaining 0.1 per cent is mostly constructed with aluminium BIW, while a very small number (less than 0.01 per cent) are constructed from carbon fibre composite. The BIW of a vehicle accounts for 20 per cent of the vehicle mass, says Tata Steel. The weight of the closures (doors, bonnet and boot/rear hatch), chassis (suspension parts) and driveline bring the total amount of steel and other ferrous metals to more than 60 per cent.
Tata Steel reports that, in recent years, the amount of ferrous metal has declined, mostly driven by manufacturers replacing iron with aluminium for engine castings. The percentage of sheet steel per car has also dropped, mainly due to:
Higher levels of equipment, trim and sound-proofing;
- More aluminium used in wheels and suspension parts;
- More moulded plastics, especially under the bonnet.
The environmental and economic requirements for reduced fuel consumption have also led to an increase in the use of lightweight materials for components that bolt on to a conventional steel vehicle but at a cost. The following table indicates the potential weight savings of using alternative materials to steel and the additional cost involved.
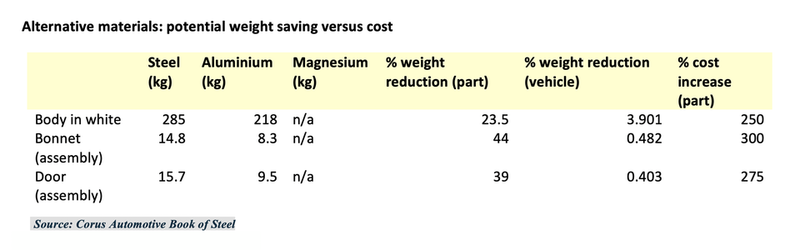
According to Bosch, a vehicle’s unitised body consists of sheet-metal panels, hollow tubular member and body panels that are joined together by multi-spot welding machines or welding robots. Individual components may also be bonded, riveted or laser-welded. Depending on the vehicle type, says Bosch, roughly 5,000 spot welds must be made along a total flange length of 1.2-2.0 metres. The flange widths are 10-18mm. Other parts, such as front bumpers, doors, bonnet and boot lid, are bolted to the body supporting structure. Other types of body construction include frame and sandwich designs.
Since 2006, the European directive End of Life of Vehicle (ELV) requires that 85 per cent of all material in new vehicles models must be recoverable. The level was raised to 95 per cent in 2015. Although the directive on ELV only specifies recovery levels for whole vehicle and not for individual components, most manufacturers are working toward ensuring their products meet or exceed the legal requirements.
In 2014, Magna International and Ford unveiled a multi-material lightweight vehicle (MMLV) concept that uses advanced material solutions to achieve a claimed almost 25 per cent weight reduction compared to the current production vehicle. The Magna-led R&D activity, in cooperation with Ford, was co-funded by the US Department of Energy. The project included engineering, prototype vehicle build and selected validation testing associated with a new aluminium-intensive passenger vehicle design architecture, facilitating an extensive use of advanced lightweight and high-strength materials, resulting in environmental and fuel economy benefits. The MMLV concept is based on the production version of a 2013 Ford Fusion and defines a new aluminium-intensive passenger car structure. The concept reduces the weight of the Fusion to that of a 2013 Ford Fiesta, making the weight of a C/D segment family sedan approximately equal to that of a subcompact B-car - two vehicle segments lighter - without compromising performance or occupant safety.
Lightweighting is a key component in Ford’s Blueprint for Sustainability, as it helps meet the goals of achieving better fuel economy for consumers while also reducing greenhouse gas emissions. In its 2015 F-150 pickup (current, still in production) Ford was bold in the use of aluminium.
Aluminium is used for the body-in-white, pickup bed and most exterior panels, but the frame is steel. Ford claims 27kg was saved in the frame and an average 320kg in the vehicle overall, compared to the previous F-150.
Ford said the weight reduction 'helped make the F-150 the company's most positive contributor to CAFE standards'. Additionally, 90 per cent of the manufacturing equipment can be reused for the next-generation F-150, reducing future capital requirements, it is claimed. And Ford says the innovation on aluminium and light weighting will pay off across a range of future Ford trucks and SUVs.
The F-150 also uses Alcoa’s 'Micromill' technology, which is described as 'more formable' than traditional automotive aluminium and therefore more design-friendly. The increased formability of Micromill aluminium makes it easier to shape into intricate forms, such as the inside panels of automobile doors and external fenders. The increased material strength allows for the use of thinner aluminium sheet without compromising dent resistance, it is claimed.
Micromill is also described by Alcoa as the fastest, most productive aluminium casting and rolling system in the world combining multiple technologies into a streamlined production system. A traditional rolling mill takes around 20 days to turn molten metal into coil; Micromill does it in just 20 minutes, it is claimed.
The next F-150 pick-up will have a new frame and aluminium panels as well as a range of fresh and updated engines. Production is scheduled to start at Dearborn Truck on 28 September.
Larger, curved screens
Jump into a new car today and you are almost sure to find a tablet-style touchscreen infotainment system positioned centre stage of the dash. It acknowledges that most of us no longer use maps to find our way around but expect the car to guide us to our destination and remain connected throughout the journey. For example, the Volvo XC90 comes loaded with semi-autonomous and connected car features, most of which are displayed on an intuitive centre console touchscreen.
As with most new technologies, what starts in the luxury market often trickles down the car segments. Inside the new Honda Civic, positioned at the top of the piano-black finish centre console - and drawing the eye as the push start is pressed - is a Honda Connect 2 seven-inch touchscreen, serving as the main point of contact to control the infotainment and climate control functions. This second-generation of Honda’s infotainment and connectivity system incorporates Apple CarPlay and Android Auto integration.
Tomorrow’s cockpits, according toHarman, will have more curved screens designed using OLED technology. The main advantage of an OLED display is that it works without a backlight, enabling it to blend into the interior.
Screens are becoming larger, too. The Tesla Model S features a huge 17-inch screen. But that is just the tip of the iceberg. China’s Byton has debuted its first concept car. A notable feature of the electric SUV is a colossal 49-inch screen stretching the width of the dash.
Whether or not such high-tech wizardry will actually make it onto the road, the above concepts demonstrate the direction the auto industry is taking.
Voice recognition
While giving instructions in our cars is nothing new, putting questions to the likes of Alexa and Cortana while on the road is. Automakers are fast adopting virtual assistants, confirming that speech is becoming the preferred interface for tomorrow’s cockpit.
Voice recognition is seen by some as the answer to eliminate many controls that have traditionally been manually operated. Voice can play an important part of a multimodal HMI solution for inputting information or for cutting through layers on the menus by requesting a function directly. Traditional voice control was centred on a set of fixed commands with catatonic responses which required some level of driver training prior to operation of the system. With the advent of the new low power, high performance microprocessors, smarter voice command engines linked into the HMI logic are now available. Even natural language and grammatical analysis are becoming more achievable.
Voice recognition, although already an option, looks set to play a bigger role as cars gradually become more autonomous.
Gesture recognition
Looking down at a touchscreen (without haptic feedback) can be distracting. Gesture recognition is therefore said to be the Next Big Thing, regarded as the logical next step from touchscreens and buttons. Gesture control operates via a stereo camera within the cabin that can recognise certain hand movements for pre-programmed adjustments and functions. Rotating your finger clockwise at a screen could turn up the volume or a finger gesture could answer or decline a call. While such novelties will make life simpler for the driver, it should also simplify interior design and liberate space for storage options.
Interior lighting trends
Advances have also been made in the interior lighting department. Not so long ago, interior lighting consisted of central and side headliner lights, complemented by low-level ambient lighting located mainly in the cockpit area. Today, the accent has changed, thanks to widespread use of LEDs enabling personalisation of car interiors. For example, during night time driving, the Mercedes-Benz E-Class takes on an entirely different feel thanks to the ambient interior LED lighting that can be personalised using a palette of no fewer than 64 colours. It really does start to feel like a cockpit, adding illuminating highlights to the trim, the central display, the front stowage compartment on the centre console, handle recesses, door pockets, front and rear footwells, overhead control panel and mirror triangle.