Overview: Lightweighting Matters
The three megatrends impacting the global automotive industry, namely fuel efficiency, individualisation and autonomous driving, strongly influence the shape and form of tomorrow's car. Fuel efficiency and CO2 requirements can be achieved via weight reduction. Matthew Beecham reviews some steps taken by the auto industry to use the right material for the right part in the right place.
Despite its impact on fuel consumption, the average mass of vehicles has increased over the past four decades. For example, a Ford Escort weighed in at around 880 kg in 1979 increasing to 1,000 kg in 1989 while a Focus weighed 1,100 kg in 2009 rising to 1,500 kg in 2019.
The weight increase across all vehicle segments is due to more stringent legislative requirements and changing customer demands (i.e. growing vehicle size, extra comfort, convenience, infotainment and safety features) and that, in turn, has caused an increase in weight of other components, such as brakes, engines and transmissions.
Reducing the weight of a vehicle by 100 kg lowers fuel consumption by 0.5 litres over a distance of 100 kilometres and cuts carbon dioxide emissions by 1.2 kg over the same distance. To put it another way, a 10 per cent reduction in vehicle weight can result in a 7 per cent improvement in fuel economy. Automakers are therefore driven to design lightweight cars that will meet increasing fuel efficiency requirements and satisfy consumer appetite for high-quality vehicles.
Adopting lightweight polymers and polyurethane composites to replace traditional materials such as glass and metal in exterior applications, including window glazing and body panel components, all help reduce vehicle mass while retaining strength. Such lightweighting measures are particularly important for hybrid electric, plug-in hybrid electric and longer range electric vehicles.
To reduce a car’s weight, a well-trodden path is to replace steel with lighter materials. All-aluminium and aluminium/carbon solutions already exist but, in addition to the high cost associated with such materials, they often necessitate an in-depth review of assembly and production processes, and there is a price to pay for that.
The use of plastics, aluminium, magnesium and different grades of steel are all under scrutiny by the vehicle makers in a bid to optimise factors. While the use of these materials in vehicles has significantly increased over the last five years, the use of iron is decreasing. For example, some automakers are switching from traditional iron blocks for engines to aluminium construction. Although less durable than iron, aluminium is lighter, thereby boosting fuel economy.
Lighten up
Select a caption afterwards
The VW Golf Mk7 is a prime example of the trend for lightweighting, weighing 100 kg lighter than its predecessor. A carbon fibre roof is offered on performance models thereby saving 9 kg alone. It demonstrates how far the use of carbon fibre in vehicle manufacture has come. The material is no longer the preserve of the luxury class but could soon become commonplace in mid-range segments. The car body itself is 37 kg lighter than its predecessor due to the use of new materials and manufacturing processes, including the use of laser stir welding. Hydro-formed high strength steel is used to produce the A-pillars, B-pillars, and roof rails. A magnesium inner tailgate structure for the four- and five-door models provides a 40 per cent weight-saving compared to a traditional steel equivalent. The car's body structure consists of 61 per cent high strength steel. Bake-hardened steel is used in the roof structure to reduce weight by a further 0.5 kg.
Using a material mix consisting of aluminium, high-tensile steels and magnesium, the BMW 5 Series is also 100 kg lighter than the previous model, while body strength and torsional stiffness have been increased. BMW's attention to detail is demonstrated in the cast magnesium instrument panel support, which is 2 kg lighter than the steel version used on the previous model, and the boot lid, which for the first time is made entirely from aluminium resulting in 4.2 hg weight saving. The lightweight doors weigh just 6 kg each, and 9 kg has been saved across the wheel/tyre/brake assemblies.
To reduce a car’s weight, a well-trodden path is to replace steel with lighter materials.
Increasing use of plastics and composites
As lightweighting continues to be one of the biggest challenges facing automakers today, some are increasingly turning to composite materials for weight savings, functionality and sustainability. Such lightweight composite solutions are a game changer, resulting in increased confidence and applications in the automotive industry. The use of composite materials typically results in 20 to 50 per cent weight savings. It also improves strength-to-weight ratio and increases part design freedom and material efficiency.
The trends toward the increased use of plastics in exterior and structural/functional/powertrain components have been driven by innovations in material, moulding and painting technologies, which have improved the performance and appearance of moulded plastic components as well as lowering their costs.
An increasing proportion of both structural and non-structural components are being made from plastics rather than steel. Some of the structural components include grille opening retainers, floor panels, bumpers and support beams. Non-structural components include exterior trim panels, grilles, duct systems, tail lights, fluid reservoirs, intake manifolds, valve covers and drive train components.
The design freedom that plastic offers is also key to its increased use. Not only does plastic allow for the manufacture of products that cannot be manufactured with other materials, plastic makes it possible to combine several parts, saving weight and cost. Additionally, recently introduced plastics that can withstand the hot, corrosive environment of the engine compartment are becoming more prevalent.
3D printing is also playing a role in vehicle lightweighting. Daimler proclaimed last year that its pilot for metallic 3D printing as a 'success' adding that it demonstrates ‘huge potential’ for the production of replacement parts and series production components.
To reduce a car’s weight, a well-trodden path is to replace steel with lighter materials.
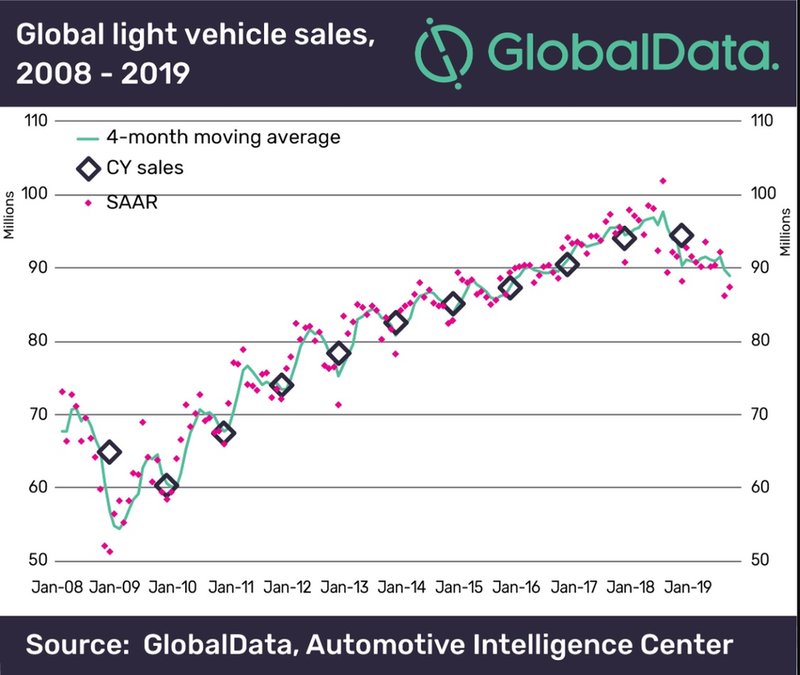
Carbon fibre– looking more promising?
Until recently, the use of carbon fibre in vehicle manufacture has been confined to high-end, low-volume vehicles - a fashionable choice for the automotive elite. Yet times are changing.
Since carbon fibre is stronger, tougher and lighter than steel, it can help increase fuel efficiency due to its lighter weight. As carbon fibre is ten times stronger than regular-grade steel yet only one-quarter of the weight, carbon fibre composites used as automotive components can help reduce vehicle weight. Yet the material is more expensive compared to traditional materials used in car production.
Cosmetic enhancements are therefore an obvious opportunity where the end customer would be willing to spend more to upgrade their car with interior and external trim components. In addition, carmakers are considering the weight saving advantages of carbon fibre for suspension components and body panels, using press and thermosetting technologies to make the processing cost element cheaper, with higher volume capability.
On balance although carbon fibre has been drawing industry attention as their lightness and strength can help the fuel efficiency of vehicles, the time-consuming work (and cost) required to produce car parts using the material remains a drawback. Despite some significant advances in developing such processes, there are still some challenges that need addressing.
Increased use of high-strength steels
While headlines are grabbed by the use of carbon-based materials or aluminium, there have been noticeable advances in the use of lightweight, high-strength steel for body panels. This is, in part, a response from steel producers alarmed by the increasing use of aluminium when the world price of steel spiked in 2011. OEMs found that high-strength steel was sometimes preferable to aluminium for certain parts of a vehicle’s body, despite its greater weight and reduced strength.
Replacing heavy steel components with high-strength steel can decrease component weight significantly. Mild steels are the most common material used in vehicle manufacture. Despite the advances made by aluminium and polymers, steel offers good value in mass production and simpler production processes than its rivals. High strength steels are typically used in a variety of applications, including floors, roof supports, side pillars and doors.
The trend in the increased use of higher strength steels such as 600 and 800 MPa material and ultra-high strength steels such as boron steel is clear, as are the weight-saving benefits.
Global market volumes of all active safety systems fitted to newly-assembled light vehicles, 2014-2034, ('000s units)
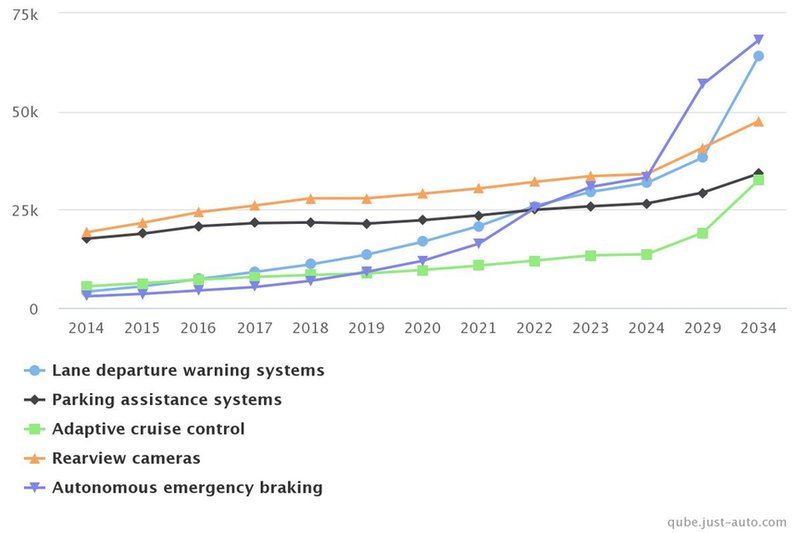
Aluminium focus
Although aluminium content in cars is increasing, albeit slowly, we should expect to see significant inroads emerging over the next few years. The automotive market has lately become the largest and fastest-growing single market sector for aluminium producers.
An increasing focus of aluminium in vehicle manufacture is the crash management area. Crash management systems consist of a bumper beam and two crash boxes that are designed to minimise the damage to the vehicle at low-speed impacts and to absorb a maximum of crash energy by deformation of higher speed impacts. Proper alloy selection ensures that crash management systems deform heavily before crack formation starts. At equal energy absorption, aluminium allows weight savings of about 40 per cent compared to steel solutions. Aluminium offers particular advantages in the crash performance combined with the overall advantage of lightweighting.
The weight is over – revival of aluminium matrix components
Lightweighting remains the holy grail of the automotive industry. Legacy materials such as high strength steels, aluminium alloys and carbon fibre all have their limitations and despite the promises made of hybrid composite metals, they haven't yet managed to break into the mainstream. But perhaps that is all about to change. Recent breakthroughs in aluminium matrix composites (AMCs), coupled with a real push from the industry to reduce weight, especially in electric vehicles, could see the potential for this family of materials to finally be relevant and crucially, viable for automotive uses. AMC manufacturer Alvant claims it could hold particular relevance to electric vehicle manufacturers.
Magnesium – a weighting game
Magnesium is the lightest structural metal. It weighs around a quarter that of steel and is 35 per cent lighter than aluminium. Hence parts made from magnesium are particularly attractive for automotive OEMs as their lower weight allows reductions in vehicle CO2 emissions.
While there has always been an appetite for magnesium in car production - particularly given the current industry requirement for lightweighting without compromising safety or performance - its application looks set to remain limited to certain parts of the car.
Typical applications of magnesium alloys in cars include steering hanger beam, wheels, cylinder head cover, intake manifold, steering wheel, tailgate inner door panel, transmission case, seat frame and inner door frame.
The cost-benefit equation remains an important consideration. The relatively high cost and energy consumption of magnesium - compared to other materials used in car manufacture - make the metal uncompetitive for most applications. Reports indicate that magnesium is sparingly used in vehicles as it is about seven times more expensive to make than steel.
Window of opportunity – thinner, lighter automotive glazing
While car window and windscreen thicknesses have been reduced, recent innovations have enabled them to be reduced further. Saint-Gobain Sekurit is supplying a lightweight windscreen for LaFerrari, Maranello’s first hybrid car. One of Ferrari’s objectives with this model was weight reduction and the glass maker enabled the car manufacturer to save 1.3 kg on the 4mm thick windscreen. Traditional windscreens are mostly 4.5mm or 5.0mm thick.
It is not often that we come across polycarbonate (PC) glazing on cars but the Citroen C3 has some. The C3 Aircross incorporates PC rear quarter windows, distinguished by a ‘Venetian blind’ white film print.
Compared to the shape limitations of glass, PC glazing is highly versatile. It is also lighter by as much as 50 per cent and boasts high impact resistance. Suppliers claim that a total weight reduction of more than 20kg is possible when replacing all glass windows (except the windscreen) for a standard minivan. The lighter weight of PC glazing is not the only benefit, however. Automakers can now consider 3D-shaped windows using PC along with innovative designs, locations and new opening and closing mechanisms.
Lighter together
Partnering between OEMs and the supply base to develop lightweight solutions remains a popular approach to meet the increasing fuel efficiency requirements. The challenge for the auto industry is for better collaboration of OEMs and their supply chain to exploit these materials for further lightweighting opportunities.
Larger, curved screens
Jump into a new car today and you are almost sure to find a tablet-style touchscreen infotainment system positioned centre stage of the dash. It acknowledges that most of us no longer use maps to find our way around but expect the car to guide us to our destination and remain connected throughout the journey. For example, the Volvo XC90 comes loaded with semi-autonomous and connected car features, most of which are displayed on an intuitive centre console touchscreen.
As with most new technologies, what starts in the luxury market often trickles down the car segments. Inside the new Honda Civic, positioned at the top of the piano-black finish centre console - and drawing the eye as the push start is pressed - is a Honda Connect 2 seven-inch touchscreen, serving as the main point of contact to control the infotainment and climate control functions. This second-generation of Honda’s infotainment and connectivity system incorporates Apple CarPlay and Android Auto integration.
Tomorrow’s cockpits, according toHarman, will have more curved screens designed using OLED technology. The main advantage of an OLED display is that it works without a backlight, enabling it to blend into the interior.
Screens are becoming larger, too. The Tesla Model S features a huge 17-inch screen. But that is just the tip of the iceberg. China’s Byton has debuted its first concept car. A notable feature of the electric SUV is a colossal 49-inch screen stretching the width of the dash.
Whether or not such high-tech wizardry will actually make it onto the road, the above concepts demonstrate the direction the auto industry is taking.
Voice recognition
While giving instructions in our cars is nothing new, putting questions to the likes of Alexa and Cortana while on the road is. Automakers are fast adopting virtual assistants, confirming that speech is becoming the preferred interface for tomorrow’s cockpit.
Voice recognition is seen by some as the answer to eliminate many controls that have traditionally been manually operated. Voice can play an important part of a multimodal HMI solution for inputting information or for cutting through layers on the menus by requesting a function directly. Traditional voice control was centred on a set of fixed commands with catatonic responses which required some level of driver training prior to operation of the system. With the advent of the new low power, high performance microprocessors, smarter voice command engines linked into the HMI logic are now available. Even natural language and grammatical analysis are becoming more achievable.
Voice recognition, although already an option, looks set to play a bigger role as cars gradually become more autonomous.
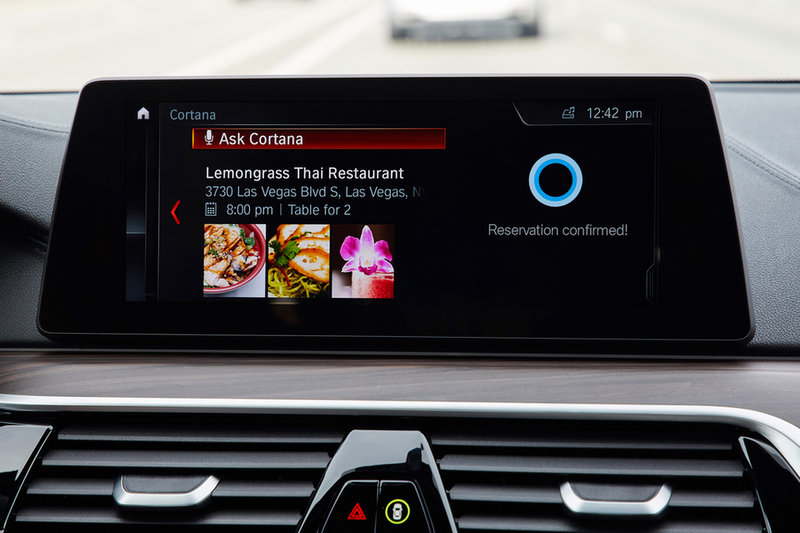
If in doubt, ask: Microsoft’s Cortana AI system forms part of BMW’s Connected Car vision.
Gesture recognition
Looking down at a touchscreen (without haptic feedback) can be distracting. Gesture recognition is therefore said to be the Next Big Thing, regarded as the logical next step from touchscreens and buttons. Gesture control operates via a stereo camera within the cabin that can recognise certain hand movements for pre-programmed adjustments and functions. Rotating your finger clockwise at a screen could turn up the volume or a finger gesture could answer or decline a call. While such novelties will make life simpler for the driver, it should also simplify interior design and liberate space for storage options.
Interior lighting trends
Advances have also been made in the interior lighting department. Not so long ago, interior lighting consisted of central and side headliner lights, complemented by low-level ambient lighting located mainly in the cockpit area. Today, the accent has changed, thanks to widespread use of LEDs enabling personalisation of car interiors. For example, during night time driving, the Mercedes-Benz E-Class takes on an entirely different feel thanks to the ambient interior LED lighting that can be personalised using a palette of no fewer than 64 colours. It really does start to feel like a cockpit, adding illuminating highlights to the trim, the central display, the front stowage compartment on the centre console, handle recesses, door pockets, front and rear footwells, overhead control panel and mirror triangle.