Driving Innovation: Accelerating the automotive seating design-to-manufacturing process
The global crisis has taken a toll on the automotive industry. To remain competitive, automotive seating system manufacturers must accelerate workflow performance, save on materials, and reduce costs. After adopting nesting tools to achieve substantial material savings, they’re turning to 3D digital solutions to improve their control and detailing in complex design processes.
How 3D digital tools help manufacturers deliver sustainable, comfortable, and safe end products
The automotive industry is constantly in motion, and it’s innovation that drives it forward. But to remain competitive, automotive component manufacturers can no longer limit themselves to standalone CAD software, they now have to become masters of digital design.
In response to the global economic crisis that’s taken a toll on the automotive industry, where textile rolls are continuously at work, there’s a critical need to accelerate workflow performance, and meet the demands for speed, flexibility, and time-to-market. Following automotive seating system manufacturers’ adoption of nesting tools to achieve significant savings on materials, they’re now contemplating 3D digital solutions to improve the control and detailing required for their complex design processes.
From design to manufacturing, 3D tools transform 3D objects from any CAD system into 2D production-ready pieces and markers. 2D/3D CAD/CAM solutions for the automotive industry, such as Optitex Automotive Solutions, provide robust tools to shorten the intricate seating design and production workflow. For example, modelling car seats in a virtual 3D environment, enables users to input and evaluate various parameters, but without the time constraints of producing physical prototypes. Global automobile manufacturersuse Optitex 3D to automate their entire workflow, by creating high-quality digital pieces, and eliminating hundreds of manual steps in the process.
Optitex’s automotive seating design-to-manufacturing process is divided into three phases: PRE-PROCESSING – creating a reliable digital representation of fabrics, leathers, and technical materials. The process is initiated by conceptual design of the seat, determined by customer-specific demands, using any standard 3D design software. It’s then exported to Optitex PDS 2D/3D, an integrated 2D & 3D workspace that simplifies positioning and modifying the pieces back and forth between the two dimensions. This enables a fast and accurate flattening process that allows the faces of a 3D model to be extracted.
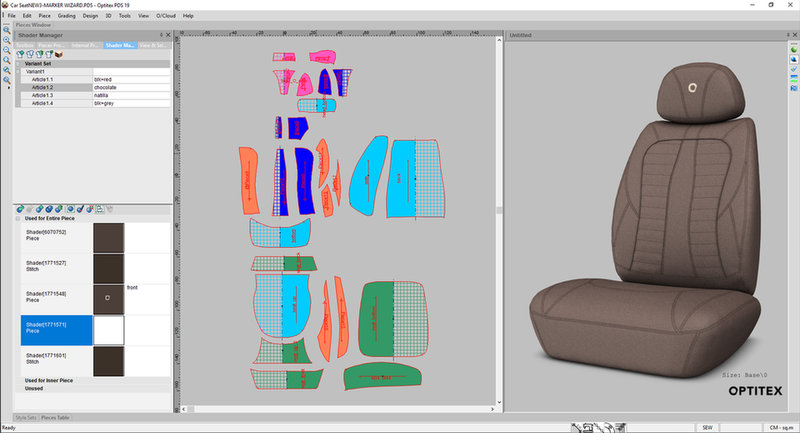
Phase two, DEVELOPMENT, creates draft pieces by flattening and importing the 3D model, and marking the surfaces. Selecting the appropriate material requires evaluating several performance indicators. Optitex Fabric Testing Solutionanalyzes the nonlinear behavior of the material, such as stretch, bend, weight, and thickness, for accurate and reliable digital representation. Pieces can be shaped and edited to conform to style requirements, and topstitching, colors, and textures, can be integrated into the final render.
Next, is Collaboration and Approval – linking design and 3D modeling, to ensure that the design intent is preserved. Optitex tools verify piece quality and accuracy using photorealistic 3D renders and physical samples, where 3D simulation tools enable multiple angle views. Pieces are then shared digitally with teams, accelerating the approval process. Optitex Marker with Nest++Pro, is an automated tool to create costing markers for material planning, calculating the amount required for production, by nesting the pieces on a cutting table. An intelligent nesting algorithm results in quality cutting layouts, and optimal material use. The output nest file, compatible with all standard cutters and plotters, exports the ready pieces for cutting, sending the data to the manufacturing floor.
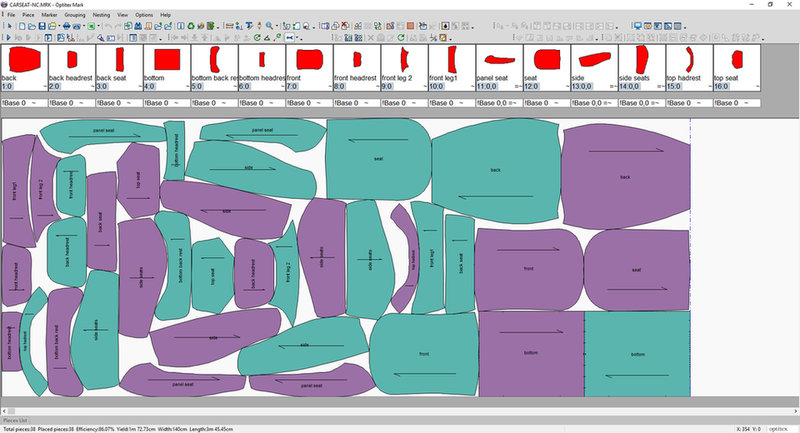
The final phase, PRODUCTION – planned according to orders, including planning cutting batches across styles and materials using Optitex CutPlan. An additional tool, Optitex Viewer, automatically views and verifies the cut pieces in actual size on a 4K screen, bypassing the need to trace, cut, and store the pieces, saving both time and storage space.
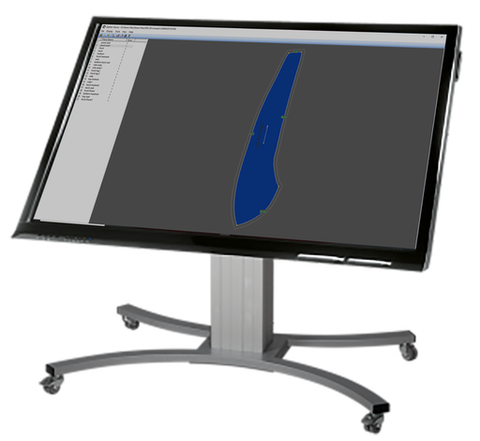
Today, more than ever, car dealers must accept new sales techniques, especially those that allow part of the purchasing process to be made remotely, said Mike Vousden, in Just-Auto, April 2020.
Optitex customer, Drive Dressy,a leading manufacturer of customized protective covers for campers and cars, use Optitex 3D technology to offer customers personalized car seat covers. Powered by Optitex, Drive Dressy customers can design their own seat covers from a series of innovative prints, or from personalized designs in a 3D configurator. Customers simply select the car brand, click "Configure Now", open the 3D configurator, and start designing.
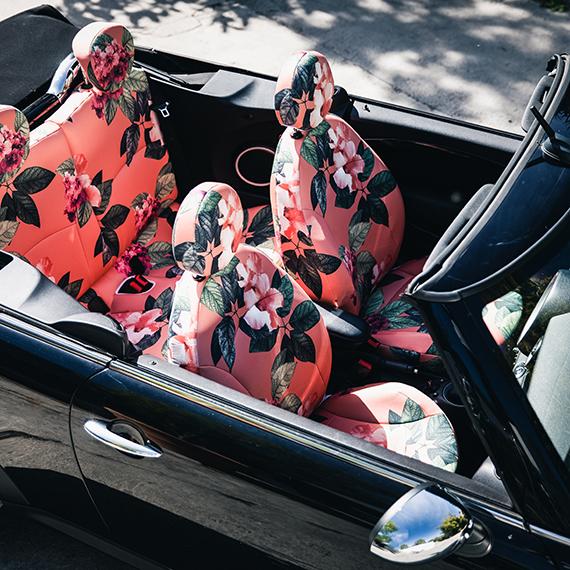
R&D Director, Jean Francois Lapetite, at French global automotive supplier, Faurecia, and valued Optitex customer for over a decade, said, “Optitex is transparent and straightforward, and material consumption and efficiency, are number 1. After material consumption, we measured compatibility, price, service, and the interface. With Optitex, we improved our overall material consumption!”
Automotive part design and production is becoming exceedingly more complex. 3D digital solutions that support the design-to-manufacturing process, remote collaboration, contain costs, and automate and validate workflows, will help build a digital enterprise designed to foster innovation.