Breakthrough in moisture
damage protection:
is it time to say goodbye to VCI?
Volatile Corrosion Inhibitors (VCI) has long been the main choice to protect metal shipments from corrosion. Yet companies who use VCI keep discovering rust damages to their metal shipments. Now, new tests conclude desiccants the safest and most efficient protection from corrosion. On top of being the most sustainable one.
Corrosion is a costly problem for automotive companies.
It occurs during transportation and will affect products, complete vehicles and components being shipped to the main manufacturing plant. It’s crucial that the shipments arrive undamaged and on time to evade delays in production. The costs if they do not are difficult to calculate. But it’s safe to say they’re significant.
For many years, the most common way to protect metal shipments from corrosion has been VCI. But it has showed unreliable and insufficient. The reason is that VCI is a reactive solution and will never give a complete protection from corrosion. The only way to achieve that is to remove excess moisture from the environment the shipped goods are placed in. This is due to the fact that it’s the moisture that is the root cause of corrosion.
Desiccants are an effective way to reduce the relative humidity in a closed environment. They’re also easy to install inside packaging or a container. Clay and silica gel are the most well-known desiccants on the market, but calcium chloride has proven to be the most efficient and sustainable alternative. In fact, AbsorGel® Calcium Chloride desiccants are so effective that they reduce the risk of corrosion to zero.
Absortech has performed different desiccant tests together with one of the leading automotive OEM’s to check the desiccant’s effectiveness. In the tests, the VCI emitters have been replaced by AbsorGel® Calcium Chloride desiccants. And in some cases, the VCI wrapping plastic has been replaced by regular wrapping plastic.
Download the report
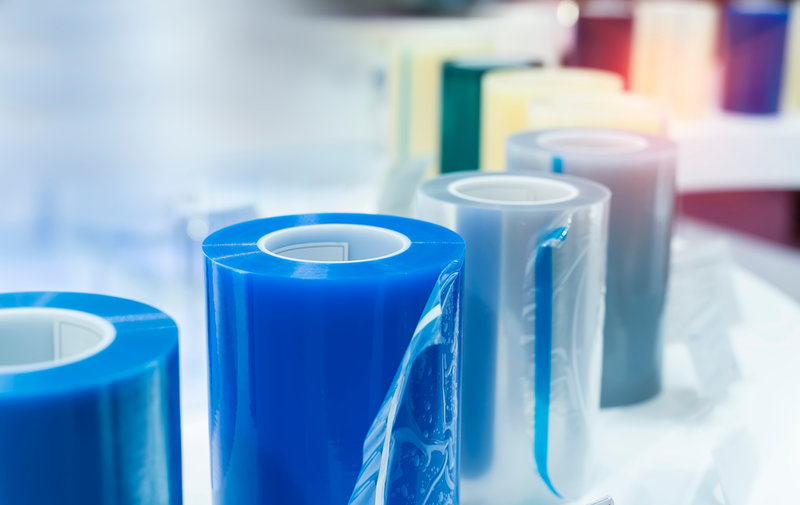
The AbsorGel® Calcium Chloride desiccants solutions have been tested in different types of packaging often used in the automotive segment: plastic box with lid, wood crates and up to seven kinds of packaging. The tests have been performed during different seasons and by train, sea and road transportation. The duration of transportation have varied from a few days up to several weeks, sometimes with long storage times after or before transportation.
The tests results represent a breakthrough in moisture damage protection in the automotive industry. Apart from its effectiveness in avoiding corrosion, the exchange of VCI for AbsorGel® Calcium Chloride desiccants means several benefits related to costs for the company and for the environment.
“Our company ships 40 000 pallets per year. With the new protection solution we will save up to 44 000 € per year and drastically reduce the amount of plastic and trash generated in our supply chain processes.”
– Quality Manager of one of the leading automotive OEM's that performed the tests.
Desiccants are a cheaper solution than common VCI components like emitters, spacers or wrapping plastic. A correct desiccant dimensioning will ensure protection during the whole shipment, even if undesired events or delays occur.
But perhaps the most beneficial outcome from the tests are the reduction of the plastic and trash generated in the shipping process. The use of calcium chloride desiccants help reduce the use of plastic by up to 80%. It will help companies become more sustainable and fulfil the targets of the United Nations Sustainable Development Goals. An important development not only for the companies who embrace this new technology, but also for the planet and future generations.
Absortech gel desiccants, called AbsorGel®, are made or calcium chloride with 94% purity. It’s a component that effectively absorbs moisture from the air. It then binds the absorbed water into a gel. The gel and the other high-quality materials eliminate the risk of leakage. Calcium chloride absorbs up to ten times more moisture than the most common alternatives on the market, such as silica gel and clay. Because of the high absorption rate of calcium chloride, the amount of desiccants needed to protect a TEU, crate or small packaging is ten times less.
This means big savings in time, handling and plastic.
”Our field tests have shown that AbsorGel® Calcium Chloride desiccants always outperform the use of VCI, both in terms of costs and environmental impact. These results are a game-changer that will change the way how automotive companies protect their components for shipping.”
– Torsten Herbach, Absortech Group Automotive Segment Leader
To exchange VCI protection for AbsorGel® Calcium Chloride desiccants is an easy process with advice from moisture damage prevention experts. A review or an on-site audit to understand the moisture prevention needs is the first step in a process that leads to a custom-made solution for your company. Our proposed solution can be validated by the conduction a field test - AbsorTest™ - with real-time monitoring with AbsorTrack™.
This process is called Peace of Moisture Mind®.
A unique Absortech procedure that helps your company save costs, handling time and the environment.
Contact Us
Breakthrough in moisture damage protection:
is it time to say goodbye to VCI?
Volatile Corrosion Inhibitors (VCI) has long been the main choice to protect metal shipments from corrosion. Yet companies who use VCI keep discovering rust damages to their metal shipments. Now, new tests conclude desiccants the safest and most efficient protection from corrosion. On top of being the most sustainable one.
Corrosion is a costly problem for automotive companies.
It occurs during transportation and will affect products, complete vehicles and components being shipped to the main manufacturing plant. It’s crucial that the shipments arrive undamaged and on time to evade delays in production. The costs if they do not are difficult to calculate. But it’s safe to say they’re significant.
For many years, the most common way to protect metal shipments from corrosion has been VCI. But it has showed unreliable and insufficient. The reason is that VCI is a reactive solution and will never give a complete protection from corrosion. The only way to achieve that is to remove excess moisture from the environment the shipped goods are placed in. This is due to the fact that it’s the moisture that is the root cause of corrosion.
Desiccants are an effective way to reduce the relative humidity in a closed environment. They’re also easy to install inside packaging or a container. Clay and silica gel are the most well-known desiccants on the market, but calcium chloride has proven to be the most efficient and sustainable alternative. In fact, calcium chloride desiccants are so effective that they reduce the risk of corrosion to zero.
Absortech has performed different desiccant tests together with one of the leading automotive OEM’s to check the desiccant’s effectiveness. In the tests, the VCI emitters have been replaced by desiccants. And in some cases, the VCI wrapping plastic has been replaced by regular wrapping plastic.
Download the report
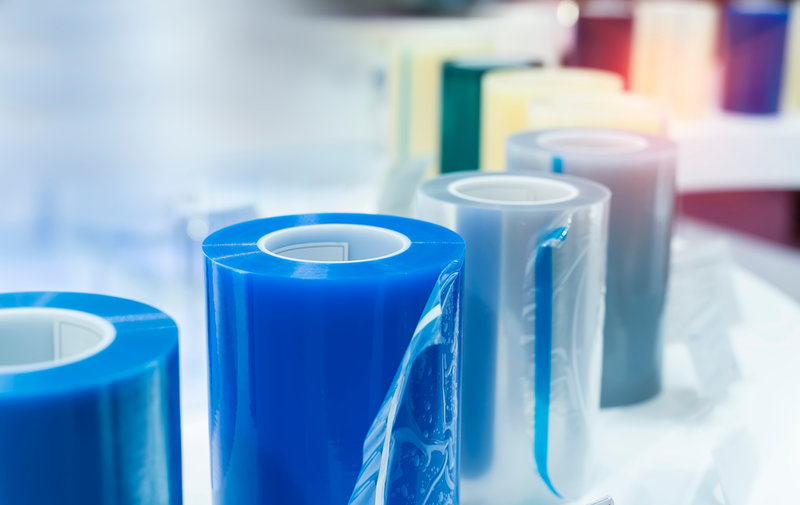
The desiccant solutions have been tested in different types of packaging often used in the automotive segment: plastic box with lid, wood crates and up to seven kinds of packaging. The tests have been performed during different seasons and by train, sea and road transportation. The duration of transportation have varied from a few days up to several weeks, sometimes with long storage times after or before transportation.
The tests results represent a breakthrough in moisture damage protection in the automotive industry. Apart from its effectiveness in avoiding corrosion, the exchange of VCI for desiccants means several benefits related to costs for the company and for the environment.
“Our company ships 40 000 pallets per year. With the new protection solution we will save up to 44 000 € per year and drastically reduce the amount of plastic and trash generated in our supply chain processes.”
– Quality Manager of one of the leading automotive OEM's that performed the tests.
Desiccants are a cheaper solution than common VCI components like emitters, spacers or wrapping plastic. A correct desiccant dimensioning will ensure protection during the whole shipment, even if undesired events or delays occur.
But perhaps the most beneficial outcome from the tests are the reduction of the plastic and trash generated in the shipping process. The use of calcium chloride desiccants help reduce the use of plastic by up to 80%. It will help companies become more sustainable and fulfil the targets of the United Nations Sustainable Development Goals. An important development not only for the companies who embrace this new technology, but also for the planet and future generations.
Absortech gel desiccants, called AbsorGel®, are made of 94% calcium chloride. It’s a component that effectively absorbs moisture from the air. It then binds the absorbed water into a gel. The gel and the other high-quality materials eliminate the risk of leakage. Calcium chloride absorbs up to ten times more moisture than the most common alternatives on the market, such as silica gel and clay. Because of the high absorption rate of calcium chloride, the amount of desiccants needed to protect a TEU, crate or small packaging is ten times less.
This means big savings in time, handling and plastic.
”Our field tests have shown that AbsorGel® desiccants always outperform the use of VCI, both in terms of costs and environmental impact. These results are a game-changer that will change the way how automotive companies protect their components for shipping.”
– Quality Manager of one of the leading automotive OEM's that performed the tests.
To exchange VCI protection for desiccants is an easy process with advice from moisture damage prevention experts. An audit of moisture prevention needs is the first step in a process that leads to a custom-made solution for your company.
This process is called Peace of Moisture Mind®.
It’s a unique Absortech procedure that helps your company save costs, handling time and the environment.
Contact Us
Breakthrough in moisture damage protection:
is it time to say goodbye to VCI?
Volatile Corrosion Inhibitors (VCI) has long been the main choice to protect metal shipments from corrosion. Yet companies who use VCI keep discovering rust damages to their metal shipments. Now, new tests conclude desiccants the safest and most efficient protection from corrosion. On top of being the most sustainable one.
Corrosion is a costly problem for automotive companies.
It occurs during transportation and will affect products, complete vehicles and components being shipped to the main manufacturing plant. It’s crucial that the shipments arrive undamaged and on time to evade delays in production. The costs if they do not are difficult to calculate. But it’s safe to say they’re significant.
For many years, the most common way to protect metal shipments from corrosion has been VCI. But it has showed unreliable and insufficient. The reason is that VCI is a reactive solution and will never give a complete protection from corrosion. The only way to achieve that is to remove excess moisture from the environment the shipped goods are placed in. This is due to the fact that it’s the moisture that is the root cause of corrosion.
Desiccants are an effective way to reduce the relative humidity in a closed environment. They’re also easy to install inside packaging or a container. Clay and silica gel are the most well-known desiccants on the market, but calcium chloride has proven to be the most efficient and sustainable alternative. In fact, calcium chloride desiccants are so effective that they reduce the risk of corrosion to zero.
Absortech has performed different desiccant tests together with one of the leading automotive OEM’s to check the desiccant’s effectiveness. In the tests, the VCI emitters have been replaced by desiccants. And in some cases, the VCI wrapping plastic has been replaced by regular wrapping plastic.
Download the report
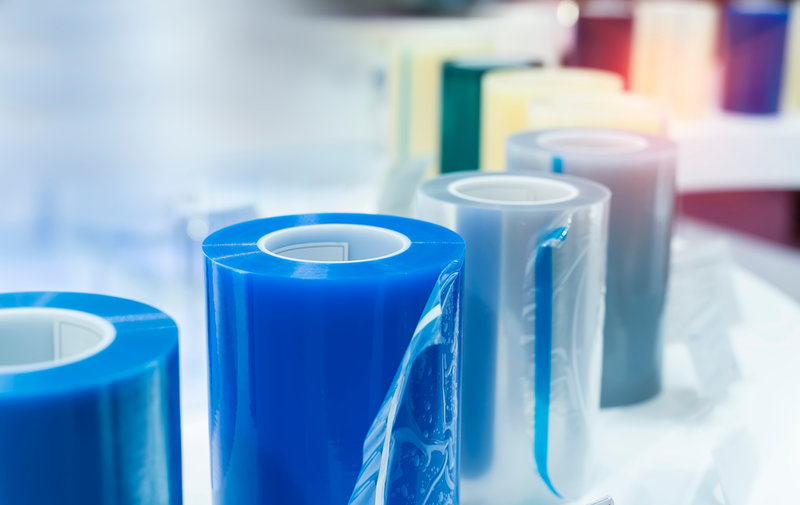
The desiccant solutions have been tested in different types of packaging often used in the automotive segment: plastic box with lid, wood crates and up to seven kinds of packaging. The tests have been performed during different seasons and by train, sea and road transportation. The duration of transportation have varied from a few days up to several weeks, sometimes with long storage times after or before transportation.
The tests results represent a breakthrough in moisture damage protection in the automotive industry. Apart from its effectiveness in avoiding corrosion, the exchange of VCI for desiccants means several benefits related to costs for the company and for the environment.
“Our company ships 40 000 pallets per year. With the new protection solution we will save up to 44 000 € per year and drastically reduce the amount of plastic and trash generated in our supply chain processes.”
– Quality Manager of one of the leading automotive OEM's that performed the tests.
Desiccants are a cheaper solution than common VCI components like emitters, spacers or wrapping plastic. A correct desiccant dimensioning will ensure protection during the whole shipment, even if undesired events or delays occur.
But perhaps the most beneficial outcome from the tests are the reduction of the plastic and trash generated in the shipping process. The use of calcium chloride desiccants help reduce the use of plastic by up to 80%. It will help companies become more sustainable and fulfil the targets of the United Nations Sustainable Development Goals. An important development not only for the companies who embrace this new technology, but also for the planet and future generations.
Absortech gel desiccants, called AbsorGel®, are made of 94% calcium chloride. It’s a component that effectively absorbs moisture from the air. It then binds the absorbed water into a gel. The gel and the other high-quality materials eliminate the risk of leakage. Calcium chloride absorbs up to ten times more moisture than the most common alternatives on the market, such as silica gel and clay. Because of the high absorption rate of calcium chloride, the amount of desiccants needed to protect a TEU, crate or small packaging is ten times less.
This means big savings in time, handling and plastic.
”Our field tests have shown that AbsorGel® desiccants always outperform the use of VCI, both in terms of costs and environmental impact. These results are a game-changer that will change the way how automotive companies protect their components for shipping.”
– Quality Manager of one of the leading automotive OEM's that performed the tests.
To exchange VCI protection for desiccants is an easy process with advice from moisture damage prevention experts. An audit of moisture prevention needs is the first step in a process that leads to a custom-made solution for your company.
This process is called Peace of Moisture Mind®.
It’s a unique Absortech procedure that helps your company save costs, handling time and the environment.
Contact Us