Technology briefing - batteries
Forget range anxiety. Electric vehicles (EVs) that can travel for more than 100 miles on a single charge are commonplace. A growing concern nowadays is charge point anxiety; will you be able to find an unoccupied, functional charger at your destination that is quick and easy to use. Matthew Beecham assesses why the tide is changing and steps being taken to lift the mood on EV charging.
Competing chemistries and construction methods vie to become the new industry standard as players race to squeeze more capacity and longevity out of their products while also battling to reduce the cost of production. What is the promise of solid-state?
Sector leaders
▪Technology: EV batteries are defined by cutting-edge technology and economies of scale. As a result, leading EV battery makers such as CATL, LG Chem, Samsung SDI, Panasonic or BYD are vast entities with huge resources to call upon. On the other hand, smaller firms are racing to develop industry-beating technology, especially in the field of solid-state batteries with the leaders being 24M, Prologium Technology, QuantumScape and Sila Nanotechnologies.
▪Manufacturing: It’s one thing to design the next generation of batteries, but it’s quite another to manufacture them at a scale and cost that suits the automotive industry. While some firms are looking to license their technology, others are building their own capacity. Leaders include CATL, LG Chem, Panasonic and Samsung SDI.
▪Investment: EV R&D demands significant capital expenditure. The companies that command the most capital can employ the best scientists, purchase the best equipment, and operate in the best locations. The largest battery companies account for the majority of investment – CATL, LG Chem, Panasonic and Samsung SDI.
As far as 2020 is concerned much depends on prospects for the economy and measures that Beijing may introduce to stimulate demand.
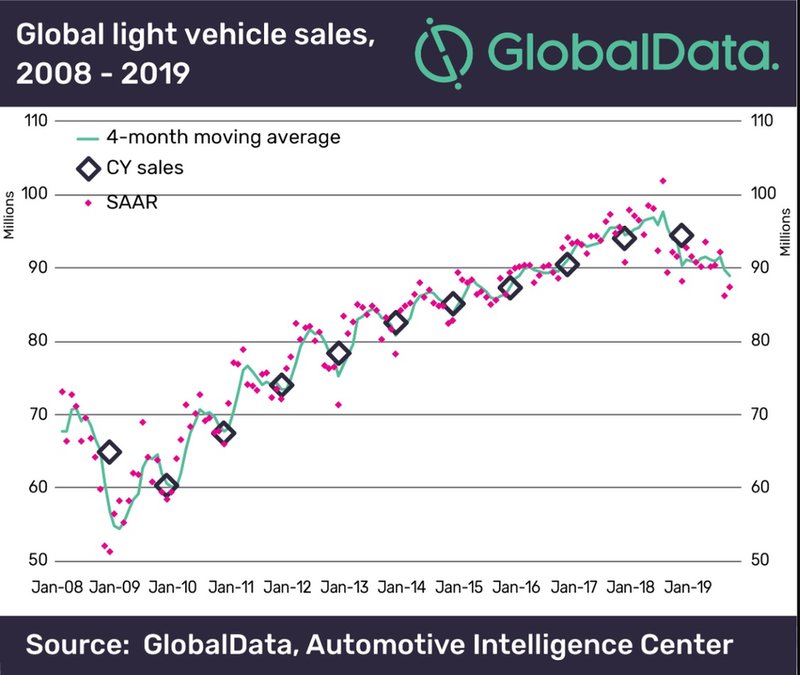
Lithium-ion batteries
Lithium-ion batteries are the current standard for portable energy storage, whether that’s in an electric car, a smartphone or a wall-mounted power pack to supplement a house’s energy demand. Compared with lead acid or nickel-metal-hydride-based batteries, lithium-ion (Li-ion) cells can store more energy for a given weight and volume, and permit faster recharging and discharging. These properties make them ideal for energy storage for electric vehicles where great energy density in a lightweight package is essential.
As far as 2020 is concerned much depends on prospects for the economy and measures that Beijing may introduce to stimulate demand.
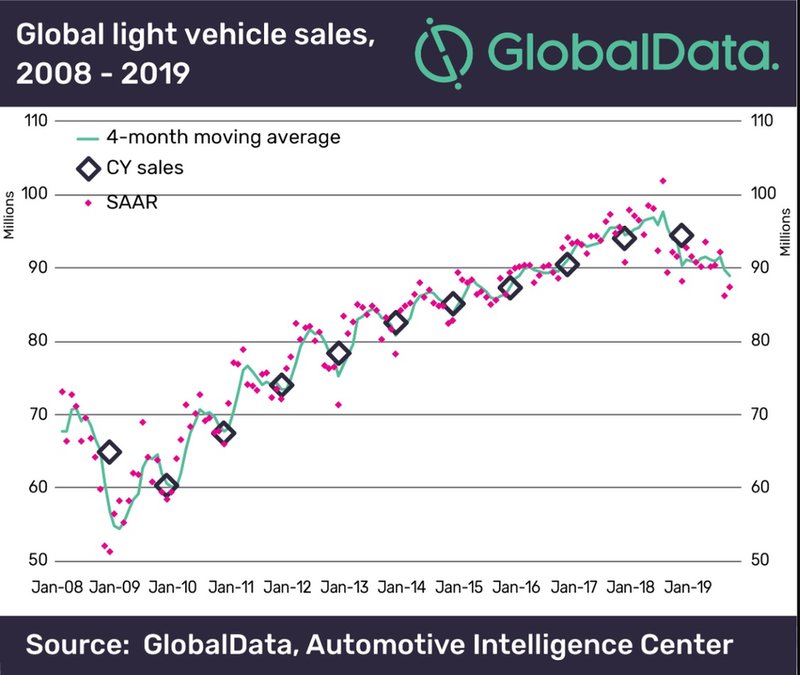
Benefits of lithium-ion batteries
Li-ion cells’ benefits are best understood by comparing them to the combustion-engined vehicles they will gradually replace. Chief among which is the fact they do not require fossil fuels to work. Consumers are increasingly aware of the damage their lifestyles inflict upon the environment and are seeking ways to reduce this. EVs produce no direct emissions of any kind and, even if they are recharged with electricity generated using fossil fuels, still do less overall environmental damage than a combustion-engined vehicle.
This is where overall energy efficiency comes into play – ie. how much stored energy can be turned by the vehicle’s powertrain into useful kinetic energy. A tank full of fuel contains a tremendous amount of chemical potential energy but, due to inefficiencies of combustion engines, only a proportion of that energy makes it to the wheels as kinetic energy, with the rest lost as heat, sound and light. The very best production combustion engines can expect to only turn between 30% and 40% of the fuel’s energy into kinetic motion, and that’s under idealized lab conditions. Electric motors, on the other hand, can achieve efficiencies of 99% or more – turning almost all the energy drawn from the battery into useful kinetic motion. As a result, while EV batteries cannot yet store as much potential energy as a tank of fuel, EVs make far better use of what little energy they can store.
As far as 2020 is concerned much depends on prospects for the economy and measures that Beijing may introduce to stimulate demand.
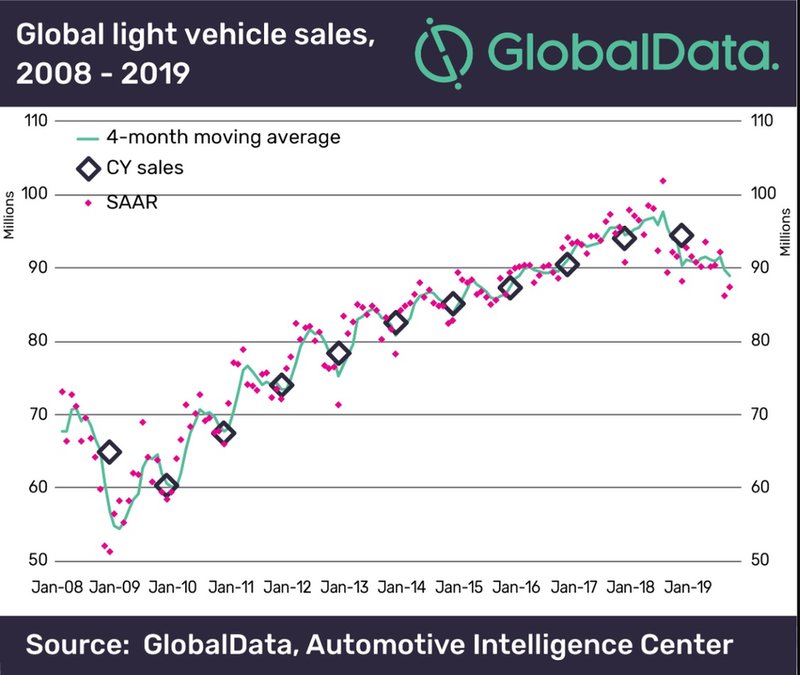
Challenges for lithium-ion batteries
There are a number of challenges that EV makers currently face in relation to the Li-ion batteries they use to power their vehicles. The primary one is cost, typically expressed as a cost-per-kWh figure. Around a decade ago, Li-ion cells cost more than $1,000 per kWh which, in an EV that might require a capacity of 80kWh or more, would push the price to unsustainable levels – acceptable in a high-margin, low-volume electric supercar but far too costly for a regular production vehicle aimed at normal consumers. Now, however, that cost has dropped below $200 per kWh and is expected to drop below $100 per kWh over the next five years. This makes larger battery packs affordable enough to fit into mainstream production EVs, allowing them to compete with combustion-powered vehicles at a similar price point.
Beyond the cost of Li-ion battery packs, EV makers must also contend with their sheer weight. Excess weight is undesirable in vehicles because it saps performance, range and energy efficiency, and battery packs account for a large proportion of an EV’s overall mass. An example of this is the Polestar 1, a plug-in hybrid coupe from Volvo’s former performance sub-brand. It’s a relatively compact car, being shorter than a BMW 3 Series but, thanks to its combination of a 34kWh battery pack, three electric motors and a traditional 2.0-litre gasoline engine, weighs more than 5,100lbs (nearly 2,400kg), despite its all-carbon-fiber body. The Tesla Model S EV is similarly hefty with its two motors and 100kWh battery pack pushing weight to more than 4,900lbs (2,200kg). In EVs where every mile of extra range is precious, reducing battery pack weight is key to improving efficiency.
Yet another challenge facing EV designers in relation to batteries is safety. While it’s true that EVs do away with the tank of explosive liquid that combustion-powered cars carry around with them, Li-ion cells can fail dramatically if subjected to dangerous environments. Specifically, the liquid electrolyte can become incredibly volatile if exposed to outside air such as during a crash or a failure of the cell’s structure. Lithium battery fires are especially violent and very difficult to extinguish, often needing to be completely immersed in water for multiple days to become fully inert. There is no evidence to suggest EV fires happen with any greater frequency than combustion-vehicle fires – they may even be statistically less likely – but EV makers will still need to reassure the public that the vehicles they build are safe. The specter of Samsung’s disastrous launch of the Galaxy Note 7 – a smartphone plagued by Li-ion battery fires – thrust the potential dangers of this battery chemistry into the public eye – a mistake that EV makers will not want to repeat.
Finally, there is a question mark over the longevity of battery pack designs. Continued cycles of charging and discharging can break down a battery’s internal structure over time, gradually reducing its storage capacity until the cell is no longer fit for purpose and must be recycled or repurposed. Active thermal control of battery packs, as found on the majority of large EVs, can mitigate this effect but the current generation of EVs have not been on the roads for long enough to know how their batteries will perform in ten of fifteen years’ time. Early Nissan Leafs – one of the first modern production EVs – used passive air-cooled battery packs and anecdotal evidence suggests that many of those models now have significantly lower maximum ranges than when they left the factory due to the breakdown of their battery packs over time. Buying an older EV only to have to replace its battery pack at great expense is likely to put off many potential EV buyers and is something manufacturers will have to work to overcome. For its part, Tesla claims to have developed a chemistry for a ‘million-mile’ battery – one that will retain its capacity for the vehicle’s entire service life – but has yet to publicly demonstrate it.
As far as 2020 is concerned much depends on prospects for the economy and measures that Beijing may introduce to stimulate demand.
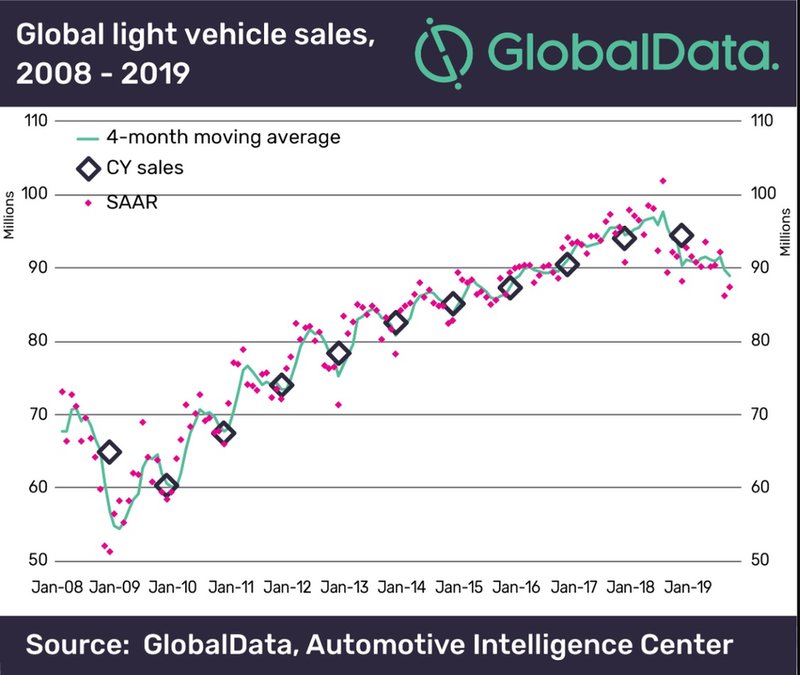
Solid-state batteries
The roots of solid-state batteries can be traced back to the 19th century when British scientist Michael Faraday demonstrated the use of silver sulfide and lead fluoride as solid electrolytes. Over the next century, development of solid-state batteries was mainly tied to laboratory experiments which, while capable of demonstrating that the technology worked, often required rare and expensive materials, or only produced cells that worked in certain specific conditions such as high temperatures, or that only worked for brief periods.
Development continued in this form for a long time but, as personal electronics became more common in the late 20th century, the demand for smaller, more powerful batteries that lasted longer than their predecessors grew. Sony introduced the first commercial lithium-ion battery in 1991 to enable its range of personal camcorders to record for longer – and this chemistry forms the basis of most batteries in today’s mobile phones, laptops and electric cars. As the phenomena of range anxiety and concerns over battery fires have grown with increased uptake of electric cars, there’s been a renewed interest in the potentially game-changing benefits that solid state batteries could bring.
As shown in the graphic below, almost all batteries follow the same design – a pair of electrodes (typically called an anode and a cathode) are suspended separately in an electrolyte. The electrolyte separates the two electrodes but permits the transfer of ions between them, and this transfer becomes the current that the battery delivers to the system.
The electrolytes in today’s Li-ion batteries generally come in the form of a liquid composed of lithium salts dissolved in organic solvents. If excess heat builds up inside the battery from overcharging, or if its casing is pierced, the electrolyte can react violently with moisture in the air causing a thermal runaway reaction that’s typically accompanied by great quantities of fire and smoke. These fires can be very difficult to extinguish because the thermal reaction can continue for a long time after it’s started.
As far as 2020 is concerned much depends on prospects for the economy and measures that Beijing may introduce to stimulate demand.
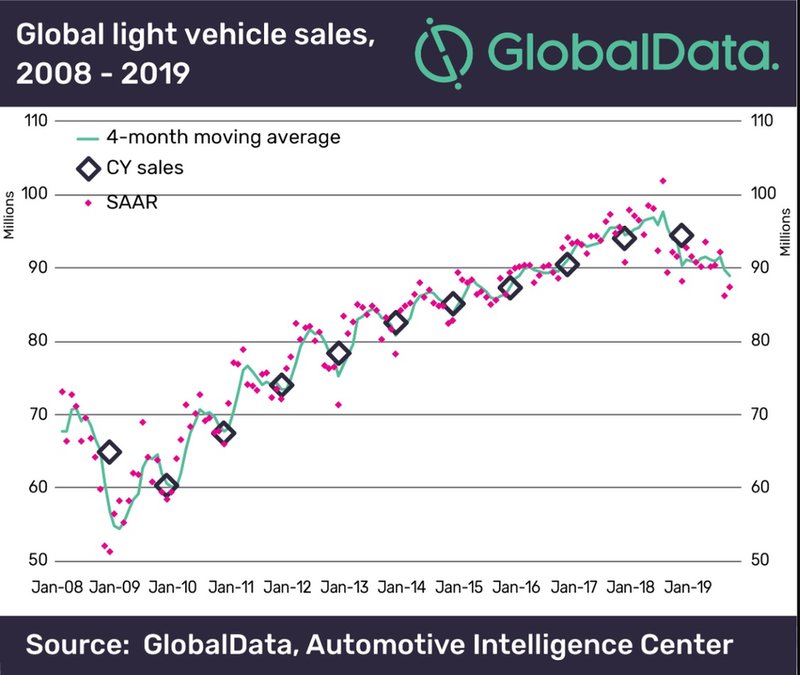
Benefits of solid-state
As the name implies, solid-state batteries replace the liquid electrolyte with a solid material. Theoretically, this brings a range of benefits including reduced pack size and weight, increased energy density (both by weight and by volume), and faster charge and discharge times. Additionally, solid electrolytes react with significantly less volatility than liquid ones when exposed to air, meaning solid-state batteries can be cut, pierced, exposed to high temperatures or generally damaged in other ways – such as a car crash – without any risk of fire.
As far as 2020 is concerned much depends on prospects for the economy and measures that Beijing may introduce to stimulate demand.
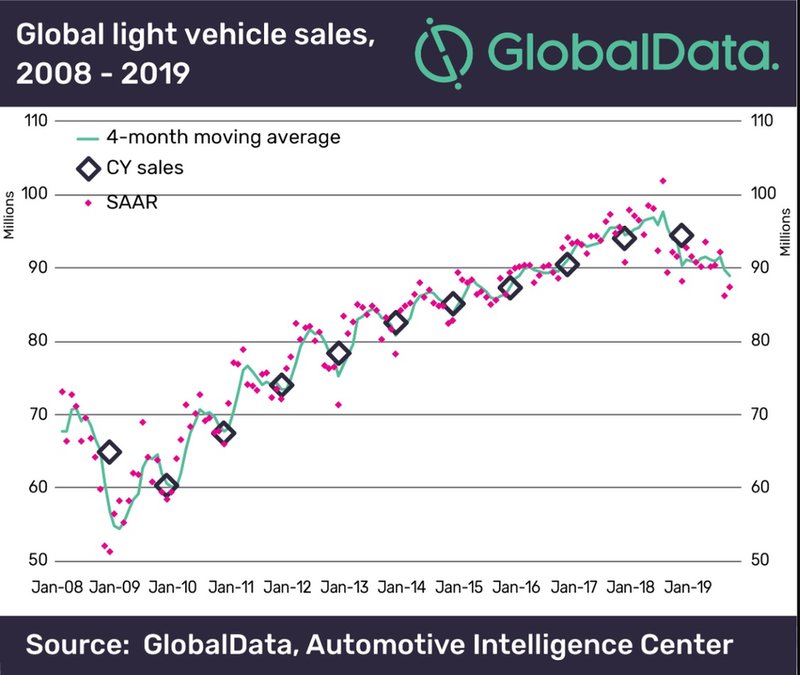
Challenges for solid-state
Before they become mainstream, however, there are a number of challenges solid-state battery designers will need to overcome. The main challenge is identifying the optimum chemical makeup of the solid electrolyte – solids generally have a lower ionic conductivity than liquids which inhibits their ability to allow current through the cell. What’s more, the chemical makeup requires materials that are cheap enough to represent a cost benefit over current lithium-ion chemistries, and abundant enough to ensure supply for potentially millions of electric vehicles. On top of this, a mass-production method must be devised that is cost effective for suppliers and carmakers, and fast enough that it can meet demand from the industry.
Furthermore, solid electrolytes will need to demonstrate their ability to remain stable over many charge cycles – potentially lasting more than a decade in the case of electric vehicles or grid-energy storage. Designers will also need to overcome difficulties in getting solid electrolytes to fully bond to solid electrodes – something that’s not an issue in liquid-based cells.
There may be a kind of half-way house solution. 24M is currently producing what it refers to as semi-solid-state batteries. Rather than use a fully solid polymer, ceramic or glass material as an electrolyte, 24M has developed a slurry mixture that incorporates the anode on one side of an electrically conductive separator, and the cathode on the other side. This solution claims to incorporate some of the benefits of solid-state technology while avoiding some of its common drawbacks.
As far as 2020 is concerned much depends on prospects for the economy and measures that Beijing may introduce to stimulate demand.
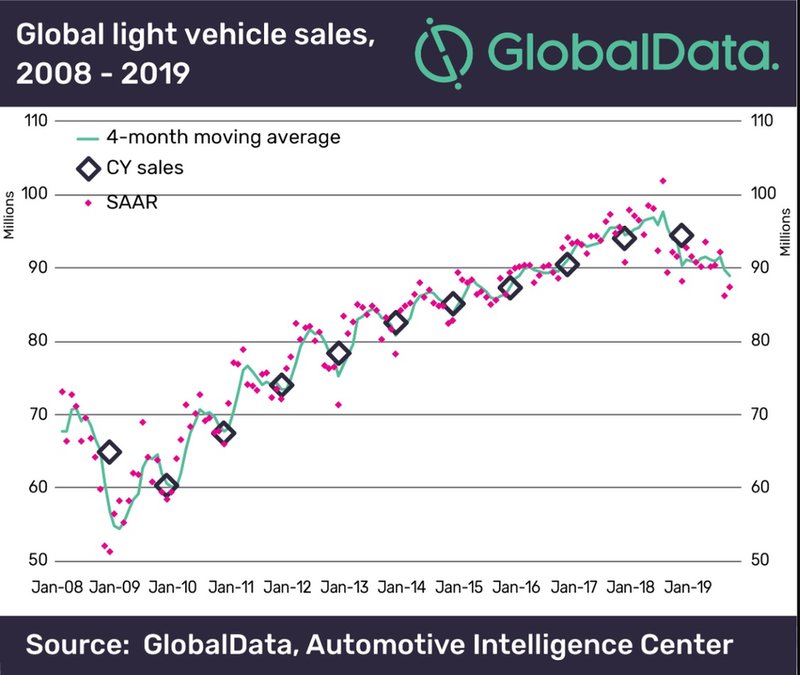
Which is better?
The question is not whether Li-ion batteries are better than solid-state ones or vice-versa, but which is the most practical option for today’s EVs. Unquestionably, at this stage, Li-ion cells are the way to go for most EV models because they are readily available, and both affordability and energy capacity are improving steadily. Solid-state cells have still never been fitted to a production vehicle and no company has yet demonstrated any ability to mass produce them at a cost or quantity comparable to current Li-ion production.
If solid-state battery cells can be perfected and produced at scale, they will probably replace Li-ion quickly due to their greater energy density, reduced weight and greater safety performance. This process will not be instantaneous though because there is likely to be a period where Li-ion cells are cheaper to produce than solid-state ones, leading to a two-lane market where high-end EVs use solid-state cells and more affordable models stick with more common Li-ion chemistries.
As far as 2020 is concerned much depends on prospects for the economy and measures that Beijing may introduce to stimulate demand.
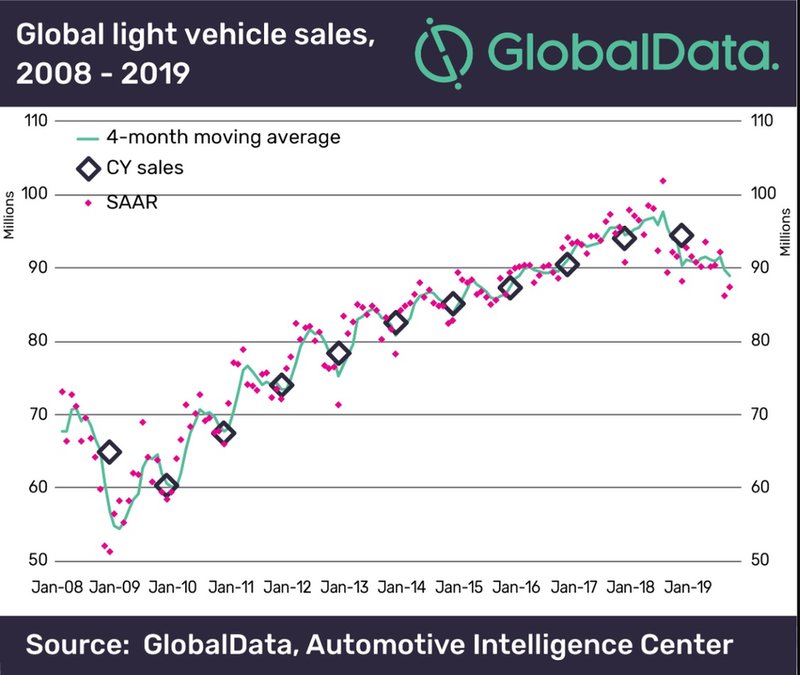
How do lithium-ion and solid-state batteries work?
The question is not whether Li-ion batteries are better than solid-state ones or vice-versa, but which is the most practical option for today’s EVs. Unquestionably, at this stage, Li-ion cells are the way to go for most EV models because they are readily available, and both affordability and energy capacity are improving steadily. Solid-state cells have still never been fitted to a production vehicle and no company has yet demonstrated any ability to mass produce them at a cost or quantity comparable to current Li-ion production.
If solid-state battery cells can be perfected and produced at scale, they will probably replace Li-ion quickly due to their greater energy density, reduced weight and greater safety performance. This process will not be instantaneous though because there is likely to be a period where Li-ion cells are cheaper to produce than solid-state ones, leading to a two-lane market where high-end EVs use solid-state cells and more affordable models stick with more common Li-ion chemistries.
As far as 2020 is concerned much depends on prospects for the economy and measures that Beijing may introduce to stimulate demand.
Gesture recognition
Looking down at a touchscreen (without haptic feedback) can be distracting. Gesture recognition is therefore said to be the Next Big Thing, regarded as the logical next step from touchscreens and buttons. Gesture control operates via a stereo camera within the cabin that can recognise certain hand movements for pre-programmed adjustments and functions. Rotating your finger clockwise at a screen could turn up the volume or a finger gesture could answer or decline a call. While such novelties will make life simpler for the driver, it should also simplify interior design and liberate space for storage options.
Interior lighting trends
Advances have also been made in the interior lighting department. Not so long ago, interior lighting consisted of central and side headliner lights, complemented by low-level ambient lighting located mainly in the cockpit area. Today, the accent has changed, thanks to widespread use of LEDs enabling personalisation of car interiors. For example, during night time driving, the Mercedes-Benz E-Class takes on an entirely different feel thanks to the ambient interior LED lighting that can be personalised using a palette of no fewer than 64 colours. It really does start to feel like a cockpit, adding illuminating highlights to the trim, the central display, the front stowage compartment on the centre console, handle recesses, door pockets, front and rear footwells, overhead control panel and mirror triangle.